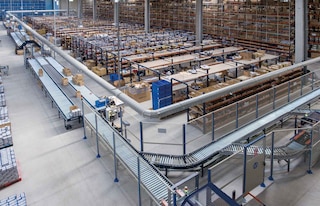
Warehouse Optimization: Systems that maximize your storage capacity
You may be starting with a completely blank canvas for your warehouse layout, or possibly looking for improvement options in a current facility. Either way, striving for an optimized design with a seamless flow of materials that maximizes productivity is the ultimate goal.
High density storage systems for warehouse optimization
Does your current layout feel cramped? Perhaps you haven’t considered all of your options when it comes to racking types, aisle widths and product picking strategies. Here we bring to light the various advantages and defining features of popular techniques for maximizing the potential of your storage facility and tackling the challenges of space utilization and picking optimization.
How different storage racks can help you optimize your warehouse
Pallet Racks
- Allow for direct access to goods
- Have adaptable designs for wide ranges of product weights and dimensions
- Available with either bolted or welded frames
- Composed of certified high-strength steel
Drive-in pallet racks
- Have single-sided entry points
- Utilize the LIFO system (the last load to enter is the first to be picked)
- Ideal solution to act as a buffer for temporary storage
- Preferred for high volume, low SKU inventory
Drive-thru pallet racks
- Have double-sided entry points (one in the back for product entry and one in the front for product removal)
- Utilize the FIFO system (the first load to enter is the first to be picked)
- Racking units may act as an intermediate between two points of the production process
- Preferred for high volume, low SKU inventory
Mezzanines
- Excellent complement to racking units in order to double or even triple storage surface area
- Economical solution to increase storage space without a building expansion
- Ideal for irregularly shaped products
- Can serve as sorting or assembly areas
- Fast, clean and simple installation
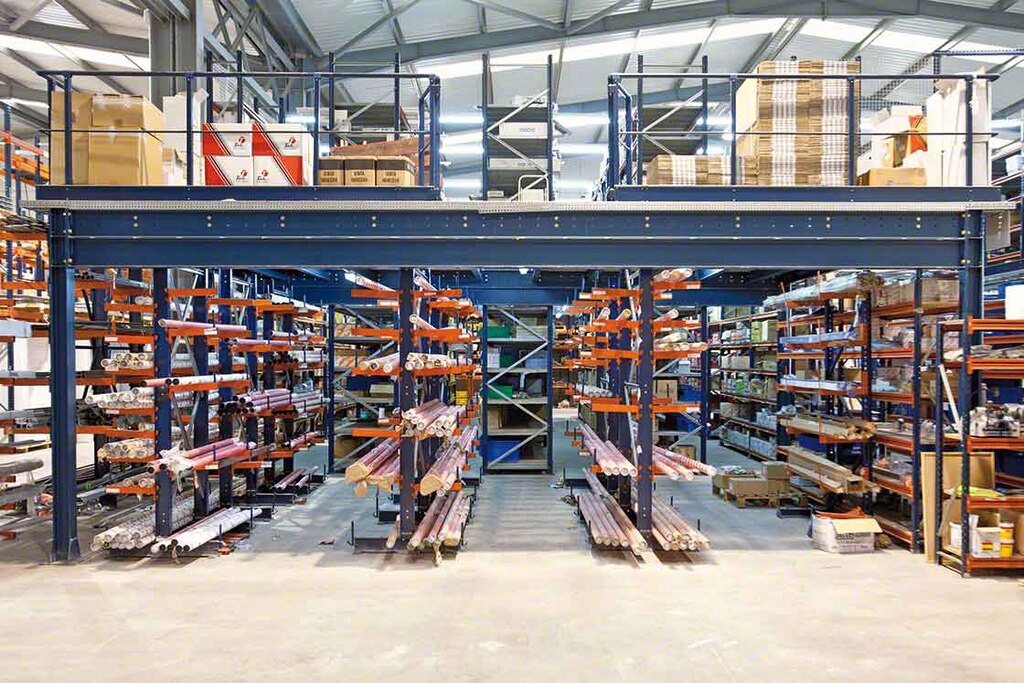
How different flow racks can help you optimize your warehouse
Pallet and carton flow racks
- Utilize the FIFO system (the first load to enter is the first to be picked)
- Pallets are introduced on one end of the strip and gravity moves them along wheel tracks towards the other end
- Ideal solution for storing high rotation perishable products with continuous flow
Push-back racks
- Utilize the LIFO system (the last load to enter is the first to be picked)
- Can be used for high consumption products
- Pallets slide along a strip of carts between the front and back of the racking unit
- The strips are arranged to slope downwards toward the front of the racking unit
Automated storage and retrieval systems
Are your racking and aisle paths optimized?
Mobile racks
- Allow for access to multiple shelves from a single working aisle
- Recommended when it is necessary to increase warehouse capacity
- Not appropriate when pallets must be moved very frequently and therefore ideal for low rotation products
- Result in highly efficient use of space, direct access to pallets and the flexibility to be able to store units of various sizes.
- Extremely cost effective for refrigerated or deep freeze storage
- Learn more about the advantages of mobile racking here.
Stacker cranes for pallets
- Can be built to over 131 feet high
- Are capable of operating in aisles only 5 feet wide
- Fully compatible with any pallet size
- Customizable system for the needs of any project
Stacker cranes for boxes
- Can reach a height of 65 feet
- Are capable of operating in aisles only 3 feet wide
- The adequate choice of fork is vital for proper functioning
- Designed to move at high speeds for increased productivity
One of the keys to warehouse planning and optimization is being able to pinpoint the precise storage systems that are best suited for the unique characteristics of your stock. Analyze shelving, flow racks and automated system options to ensure the optimal handling and distribution of your inventory. Rethink your racking layouts and aisle spaces in order to take complete advantage of the total potential your facility has to offer.