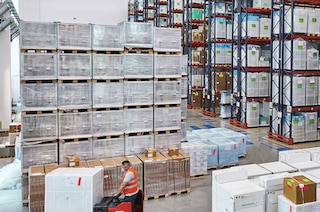
Block stacking: optimizing warehouse space without racks
Block stacking is a warehousing method in which goods are stacked directly on the floor. When this storage technique is employed properly, it can bring several logistics benefits. It’s essential to know the particular characteristics of this system and the situations in which it’s most effective in order to get the most out of it.
In this post, we’ll explain exactly what block stacking is, its advantages and drawbacks, and the difference between block and high-density storage.
What’s block stacking?
This storage technique consists of stacking unit loads (pallets, boxes, or products) one on top of the other on the floor of the warehouse, without resorting to racks.
The goods may or may not be palletized, depending on the type of product being handled. The only condition is that they be strong enough to withstand the weight of the rest of the products. Otherwise, if the product is fragile, the structure could break.
Pros and cons of block stacking
Block stacking in a warehouse brings the following benefits:
- Cost savings: this is probably the main plus point. Block stacking is the most economical technique of all, as it doesn’t require racks.
- Space maximization: space is optimized by eliminating unnecessary aisles, as is volume, by stacking the loads (as compared to placing only one pallet on the floor).
- SKU management: for block stacking to be efficient, it’s crucial to form high-density groups of a single SKU. This serves to control the stock and easily locate each product.
On the other hand, block stacking does have some significant disadvantages that we need to take into account, for instance:
- Height limitations: this depends on the type of load stored. That is, if a large amount of product is stacked, the structure could become unstable and collapse. Only racks can guarantee storage of loads at great height.
- Damage to goods: if the weight of the stacked load is excessive, the merchandise located on the lower levels could become damaged.
- Risk of accidents: racks are sturdy and remain intact, minimizing impacts from handling equipment and ensuring total stability of the loads they hold. By contrast, block stacking doesn’t have these benefits, making it more prone to risks and accidents.
Generally speaking, the primary advantage of this storage method is its low initial investment. However, to ensure the physical integrity of the goods and the operators, racks are a must.
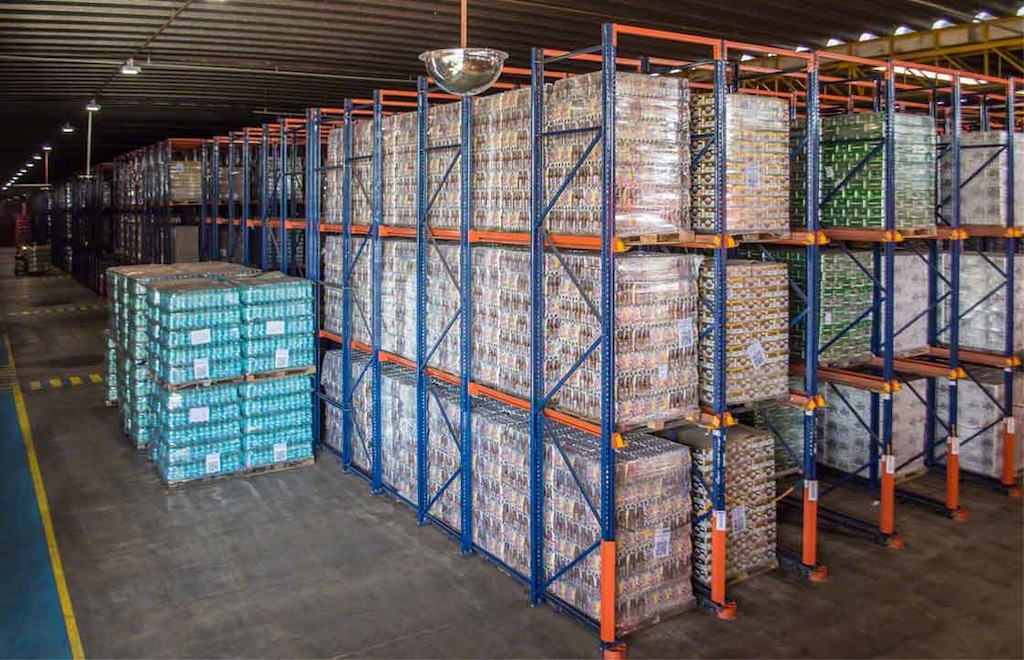
When to set up block stacking in your warehouse
Each storage technique has its pros and cons and, obviously, is subject to the space available, the type of goods handled, and the movement flows required, among other factors. On that basis, block stacking is focused on companies that work with goods prepared to be stacked, saving costs and simplifying operations.
Another key aspect has to do with stock turnover. Block stacking can only be used with low-turnover merchandise: the fewer goods inflow and outflow operations, the greater the stability of the structure.
Block stacking is most common when a company’s investment capacity is limited and it has a space for setting up homogeneous blocks of goods. When businesses have the necessary capital, they normally purchase storage systems to maintain the integrity of the products.
Lastly, block stacking is employed in conventional warehouses for cross-docking operations or as a temporary storage buffer. This is used to temporarily store products pending sorting, storage, or dispatch without being processed through the storage area. This is the case of Brazilian company Refrescos Bandeirantes; we carried out a project for this firm in which pallets are stored in blocks before being placed in drive-in/drive-through pallet racks. That is, the solution combines racks with occasional block stacking.
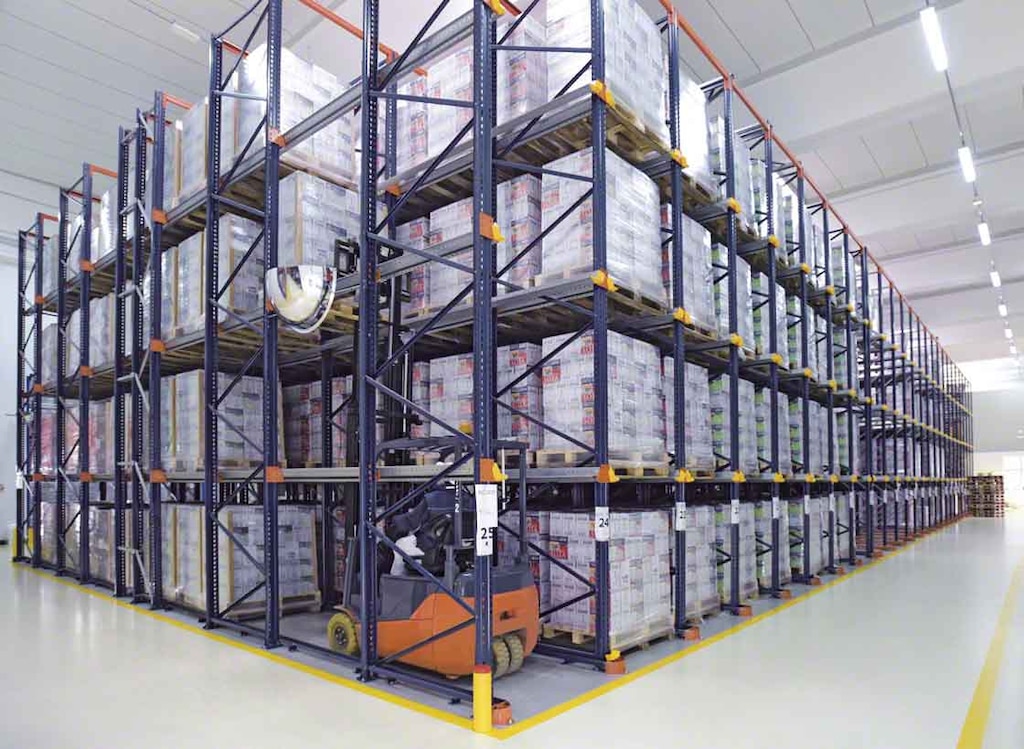
Differences between block stacking and high-density storage
Block stacking and drive-in/drive-through storage systems both store merchandise in a compact way. The difference between them, though, is notable: drive-in/drive-through systems use racks to support the loads, while block stacking, as the term suggests, consists of placing one load on top of the other. The racks in any high-density system are equipped with protection elements that ensure the complete safety of the goods and the operators.
There are various types of high-density storage systems, although — as with block stacking — they are all noted for doing away with aisles to optimize storage space. The most basic of all comprises drive-in/drive-thru racks, whereby forklifts handle the pallets by operating inside the racking.
Meanwhile, the Pallet Shuttle system uses shuttle powered by an electric motor to insert and remove loads from the racks. Replacing forklifts with the shuttle considerably reduces handling times and the risk of accidents. Finally, we have Movirack mobile racking systems, in which racks are installed on mobile bases to open the selected working aisle and provide direct access to all the goods.
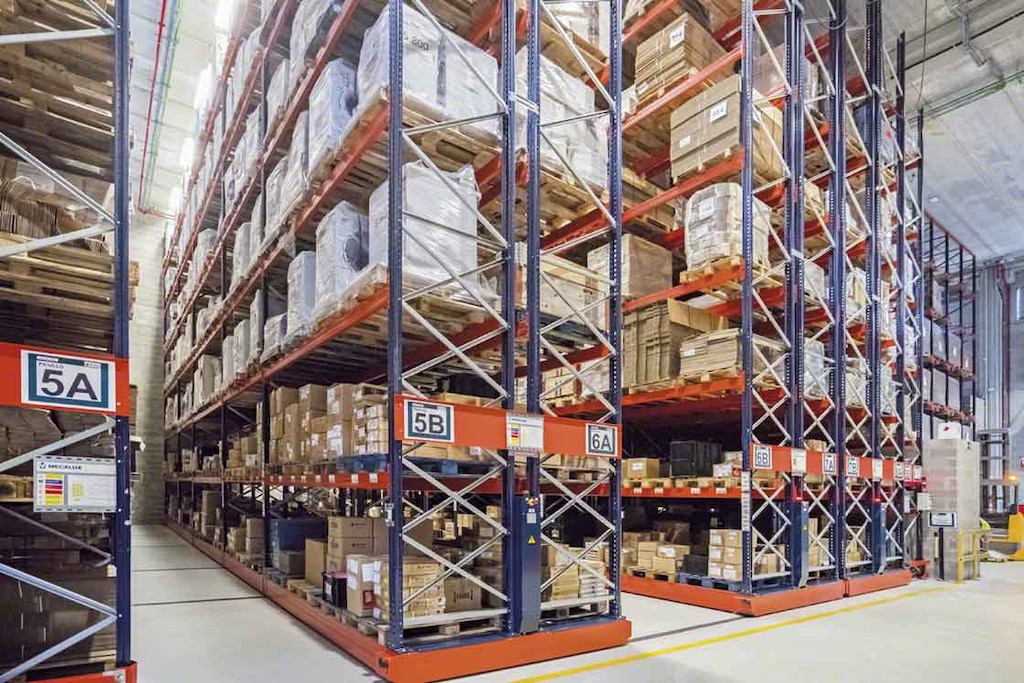
Find the best solution: know your needs
Block stacking can be beneficial at times, provided you’ve carefully analyzed each and every one of its advantages, risks, possible situations, etc. It’s a storage method that’s attractive for its cost effectiveness, as it doesn’t require racks. However, if put into practice badly, it can be counterproductive. The reason? It increases the risk of accident and is difficult to scale up (it can’t be employed in an automated warehouse). Nevertheless, as a technique, it can be used along with others in conventional installations for very specific purposes, such as organizing goods before ultimately inserting them in their designated slots.
If you think block stacking can meet your logistics needs but aren’t totally convinced, get in touch with Interlake Mecalux. We’ll answer all your questions and help you find a customized storage solution.