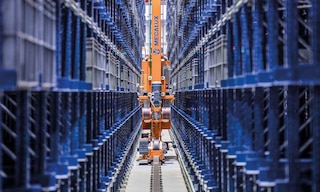
Collaborative robots and industrial robots: why use them in your warehouse?
Collaborative robots and industrial robots are two elements spearheading logistics automation. These machines streamline all warehouse operations and, most notably, eliminate the risk of mistakes stemming from manual product handling.
In this post, we delve into the main differences between collaborative robots and industrial robots, analyzing how to choose between one type of machine and the other.
Robotics in Logistics 4.0
Robots were first employed in logistics over 40 years ago, especially in industries with complex production processes and responsible for moving large load volumes. Nevertheless, Logistics 4.0 has driven technological advances such as the Industrial Internet of Things (IIoT) and machine learning. These developments have made it possible to replace large, cumbersome robots with other kinds of machines capable of optimizing processes on their own.
Thanks to these technologies, more and more logistics facilities are investing in process automation. According to a study from consulting firm ABI Research, by 2025, over 4 million robots will have been installed in 50,000 warehouses worldwide.
In a scenario of increased competition, companies have been forced to substitute manual labor with machines that automate the more repetitive or onerous tasks. The introduction of robotics has become popular in logistics processes including goods receipt and slotting (with automated systems such as the automated Pallet Shuttle and stacker cranes/AS/RS for pallets), load movements (with conveyors for boxes), and order dispatch (with sorters for shipping products by transportation route).
Using robots in the warehouse makes it possible to:
- Eliminate the risk or errors due to manual management of the goods.
- Speed up the flow of goods and load movements.
- Gain greater control over stock.
- Save warehousing space through compact storage.
- Ensure the utmost safety of the goods, the operators, and the facility.
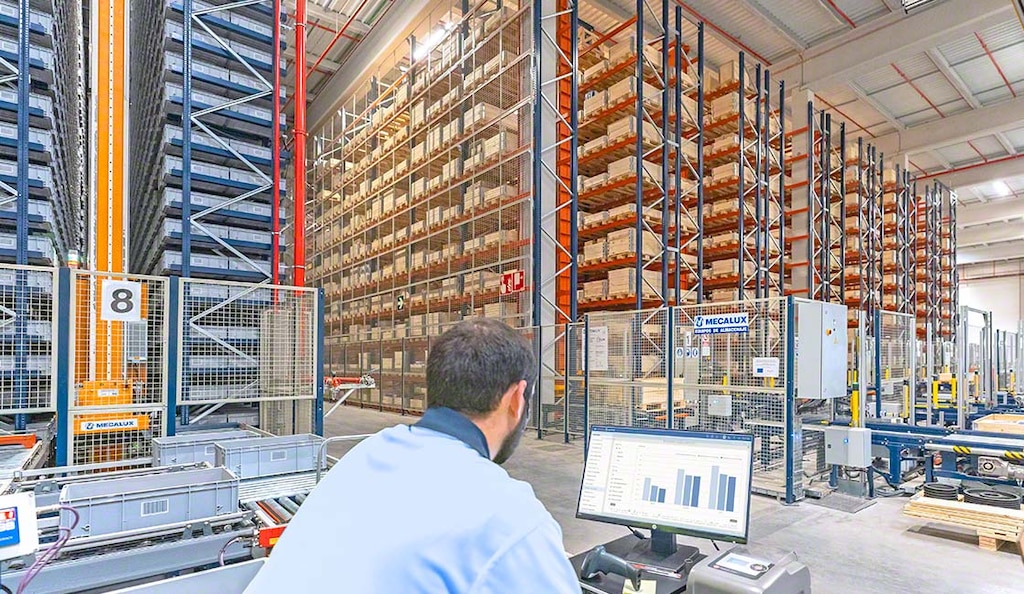
What is a collaborative robot?
Collaborative robots or cobots are machines that work alongside operators in a production line or a warehouse. Their design ensures that the operator can safely interact with the machine, guaranteeing the protection of both the worker and the goods. International standards such as ISO 10218-1 and ISO/TS 15066 establish the necessary safety guidelines for joint work between machines and operators.
Although cobotics has a strong presence in sectors requiring robust manufacturing processes, such as the automotive industry, it’s becoming an increasingly common solution in all types of businesses. In fact, collaborative robots are employed in any logistics or production operation entailing load movements that could be too burdensome for workers to handle.
Instead of replacing operators, these machines are implemented in warehouses and production centers to complement employees’ tasks and optimize their throughput. For example, collaborative robots perform actions that place the greatest strain on operators, such as order packaging and pick and place involving heavy items.
One of the best examples of cobotics in logistics is the robotic arms installed on pick stations to make order picking more agile. Another is cobots, which complement the operator when palletizing or packaging a product.
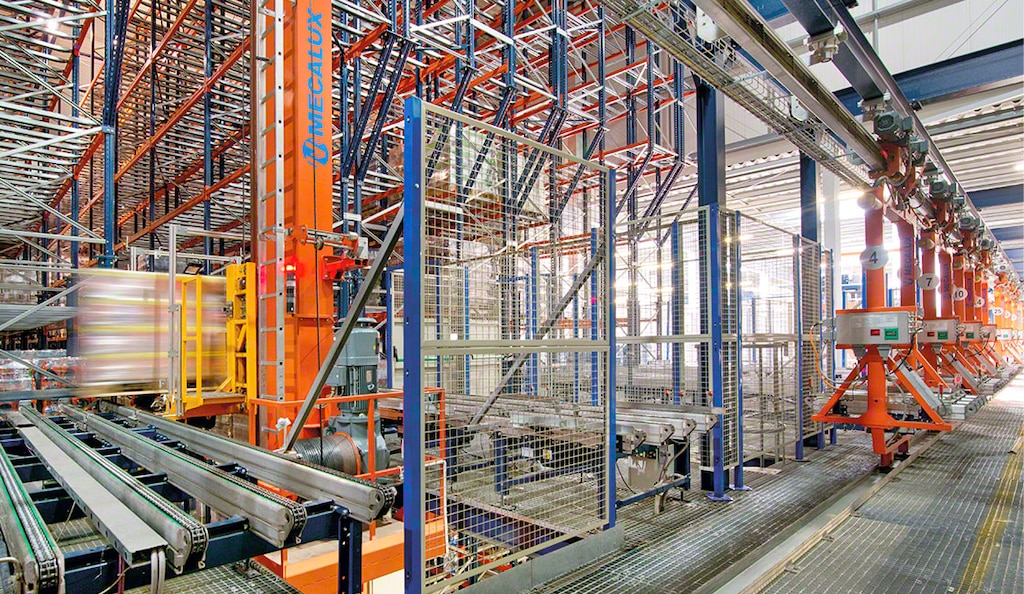
What is an industrial robot?
An industrial robot is a programmable product handling machine employed in a warehouse or production center to carry out highly specialized tasks. These include slotting and removing stock and moving large volumes of product.
The main function of industrial robots is to replace manual tasks with a single objective: to ramp up productivity, store goods in a compact way, and minimize the risk of error. This equipment stands out for its great capacity to handle goods on a mass scale (24 hours, 7 days a week) without the intervention of an operator.
This is the case of miniload systems, which feature a stacker crane located between two aisles of racking. This machine expedites the storage and removal of boxes and trays in the warehouse, without the need for human intervention. The stacker crane picks up the goods and places them in the location indicated by the warehouse management system (WMS). This, in turn, programs all the movements executed by the machine. The same goes for the extraction process: the stacker crane picks the box specified by the WMS and deposits it on the conveyor, which brings it to the pick station.
Other examples of industrial robots are pallet conveyor systems and conveyors for boxes. These can be used to create predetermined circuits that speed up the flow of goods between the different areas in the warehouse or between adjacent stations.
Reasons for choosing collaborative robots or industrial robots
Robotics ensures greater efficiency in warehouse processes. But should you go for collaborative robots or industrial robots? Your logistics planning, operations, and warehouse layout design will determine whether your manual processes should be replaced with cobots or automated storage and retrieval systems (AS/RS) such as stacker cranes and conveyors.
The first major distinction between these two types of robots is the degree to which they are specialized: industrial robots tend to be used for only one task, taking up a lot of space and following a fixed route. Cobots, meanwhile, are a flexible solution that can be relocated to different areas of the facility in line with logistics needs. Industrial robots, however, are an ideal tool for streamlining labor-intensive tasks with a constant repetition of movements, as is the case with product storage and removal.
For these reasons, logistics managers should assess whether existing demands in their particular facilities would best be served by one type of machinery or the other. A warehouse that needs to quickly move high product quantities can swap forklifts for an automated transportation system such as conveyors or electrified monorails, provided goods flows are repetitive. As opposed to collaborative robots, these machines don’t employ machine learning to carry out their functions. Instead, they operate using advanced algorithms to complete the routes assigned to them by the WMS.
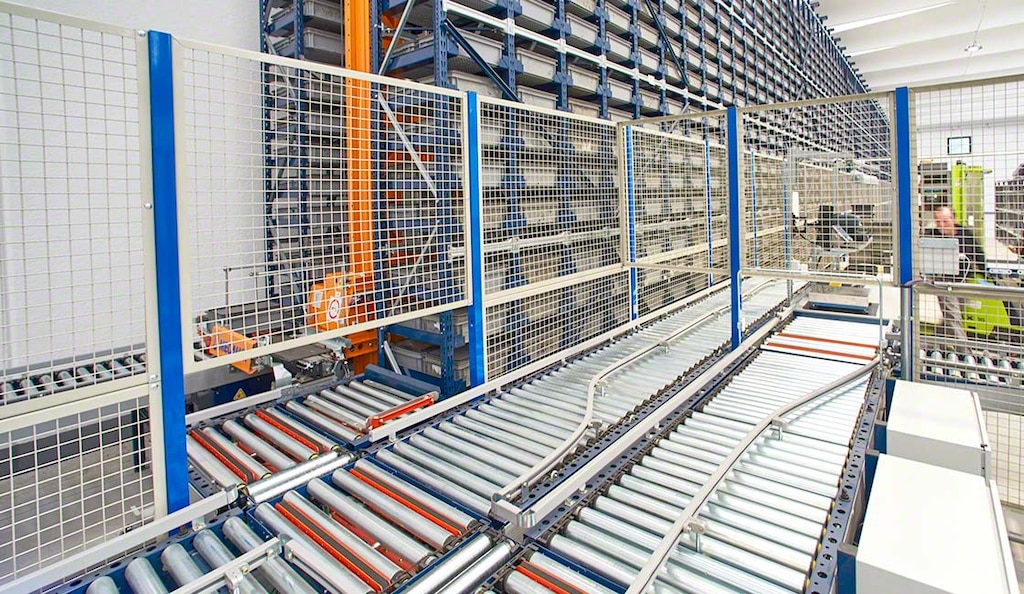
Process automation: efficiency and productivity for your warehouse
Nowadays, companies incorporate automated solutions to gain in efficiency and productivity. Both collaborative robots and industrial robots have been developed to streamline movements in facilities and optimize throughput.
Want to make your logistics operations more competitive? Don’t hesitate to contact us. One of our expert consultants will assess your situation and advise you on the best solution for your business.