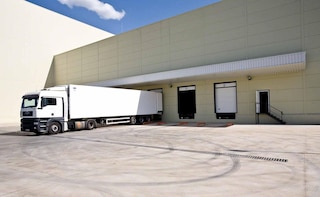
Advantages and disadvantages of cross-docking: when to apply it in your warehouse?
Cross-docking is an order fulfillment strategy that eliminates mid-stage storage of goods. Properly managed, it makes it possible to speed up the picking and dispatch of goods, reducing operating costs.
However, in what situations does it prove to be an effective tactic? What are the advantages of cross-docking in a warehouse? What are the advantages of cross-docking in a warehouse? What are the risks associated with this practice? Let's take a closer look at the answer to these questions:
Main advantages of cross-docking
1. Storage space occupancy savings: although an area must be reserved in the warehouse allocated to controlling and conditioning incoming goods, cross-docking frees up core storage space. Inventory cost savings is a benefit linked to this point.
2. The number of operations and the handling of loads are reduced: unloading, quality control, order conditioning and dispatch of goods are maintained, but middle stage tasks such as picking and storage disappear. This means less risk of damaging the goods, as their handling and transport within your warehouse is reduced. Additionally, a related advantage is the increase in operator productivity.
3. It shortens delivery times and makes the supply chain more agile: cross-docking saves time when dispatching goods, as it simplifies the traditional process. This translates into improved customer service.
4. Reduces a supply chain’s carbon footprint: the impact of cross-docking leads to power savings in terms of goods transport both inside and outside the warehouse and this allows a more eco-friendly supply chain to run.
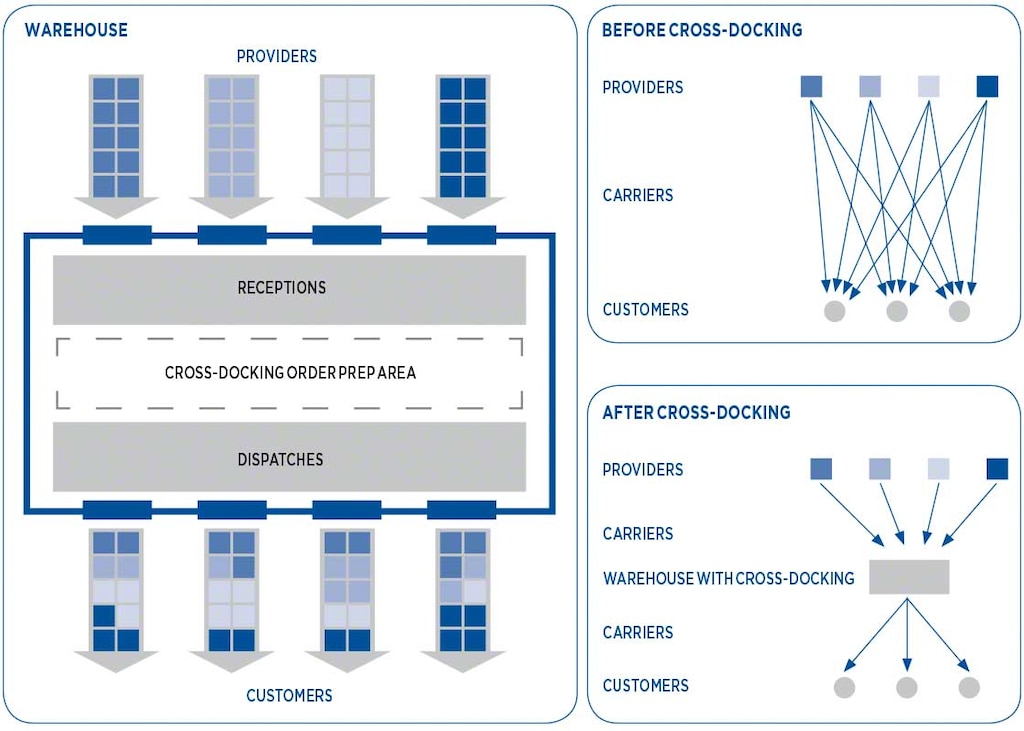
In short, well-planned cross-docking improves the overall profitability of warehouses or distribution centers that use this method thanks to the overall operational time savings that it represents.
Cross-docking risks
1. Implementing the cross-docking strategy in the warehouse involves releasing the capital to do so. This can translate into a warehouse redesign to reserve space for a conditioning area and/or the adoption or configuration of a warehouse management system to assist with cross-docking tasks.
2. It requires effective integration of the entire supply chain: this means, for example, that the labelling system between suppliers and receivers is shared and compatible. Similarly, it is necessary to connect the information systems that each player works with (fleet management software,warehouse management software, etc.).
3. It requires time for planning and coordination: without synchronization between supply and demand and proper planning, cross-docking is not recommended in the warehouse. Therefore, in the global computation, cross-docking should save enough time to cover its application in operational planning.
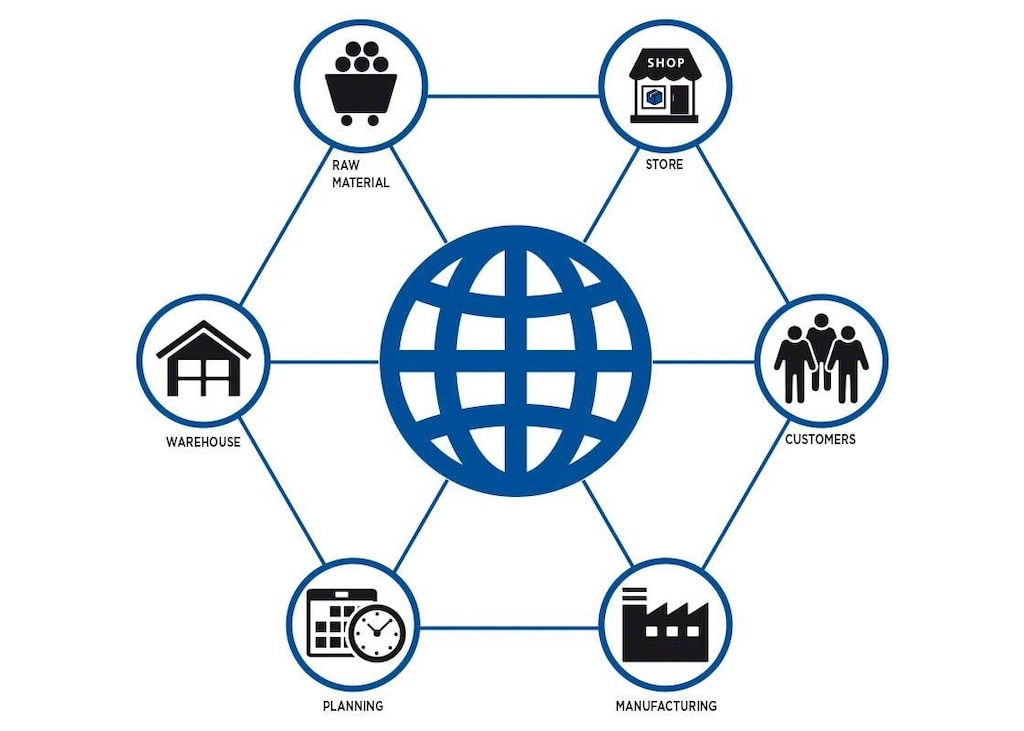
So when should cross-docking be used in the warehouse?
1. Large volumes of goods with a stable demand: flows remain constant and can be "predicted" with a small margin of error. This allows good planning of cross-docking operations and eliminates the need to store large quantities of safety stock.
2. The type of merchandise deteriorates over time or expires: for example, in the case of the food industry, products must arrive with sufficient shelf life to be put up for sale. Cross-docking, on the other hand, saves costs associated with refrigerated storage.
3. Products that are part of special promotions or rebates: Cross-docking is an effective way to respond to peaks in demand quickly. This is a very popular strategy in the consumer goods sector (retail and discount stores).
4. High-value items with tight delivery times: in the case of bulky, high-turnover items such as furniture or appliances–, the end customer demands a quick delivery. Many distribution companies avoid having a large amount of stock on hand in each specific store to save on overhead, and instead cross-docking from their distribution centers: thus, they are able to respond to demand more quickly.
All these advantages and disadvantages of cross-docking mean that it is being implemented in warehouses from sectors such as: large-scale distribution, the food sector, pharmaceuticals, chemical products and 3PLs, among others.