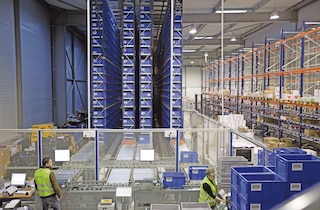
Manufacturing logistics: how to optimize it
Traditionally, manufacturing logistics has been a linear, predictable sector. For years, manufacturers represented the link between raw material suppliers and distributors. Nevertheless, the current financial backdrop has halted that trend, forcing companies to take on personalized manufacturing processes with a stock of materials as numerous as it is diverse.
Business trends such as just-in-time manufacturing, market globalization, and stringent customer demands for speedy deliveries are driving the transformation of manufacturing logistics. In this post, we define and assess the characteristics of the new manufacturing logistics scenario and work out the best strategies to make the most of it.
What’s manufacturing logistics?
Manufacturing (or industrial) logistics encompasses the management and optimization of storage processes, as well as the movement of materials in installations connected to a production center. In short, it includes all logistics processes that take place from the purchase of raw materials to the creation of the product.
Snapshot of production processes
To better understand how manufacturing logistics works, let’s briefly go over the two most common production systems and the role they play:
- Make to stock, or the push system
This takes place when there is wide demand for the final product and it has standard features that don’t include any kind of personalization. In this case, production centers manufacture the items in advance. These goods are sent directly to the warehouse; thus, the sales department only sells the stock available in the warehouse (as opposed to the pull system, which we’ll examine below).
- Make to order, or the pull system
The pull system works the other way around: the production center manufactures the goods once it receives the orders from the customers. These are given a set delivery date. With this method, even though no finished products are stocked, the company can maintain an inventory of semi-finished goods; this shortens delivery times once the customer’s order has been placed.
Although certain sectors tend to employ one manufacturing system over another, the truth is, both can be used. For example, in the automotive sector, standard cars are manufactured (push system), as are other vehicles on demand with customized features (pull system).
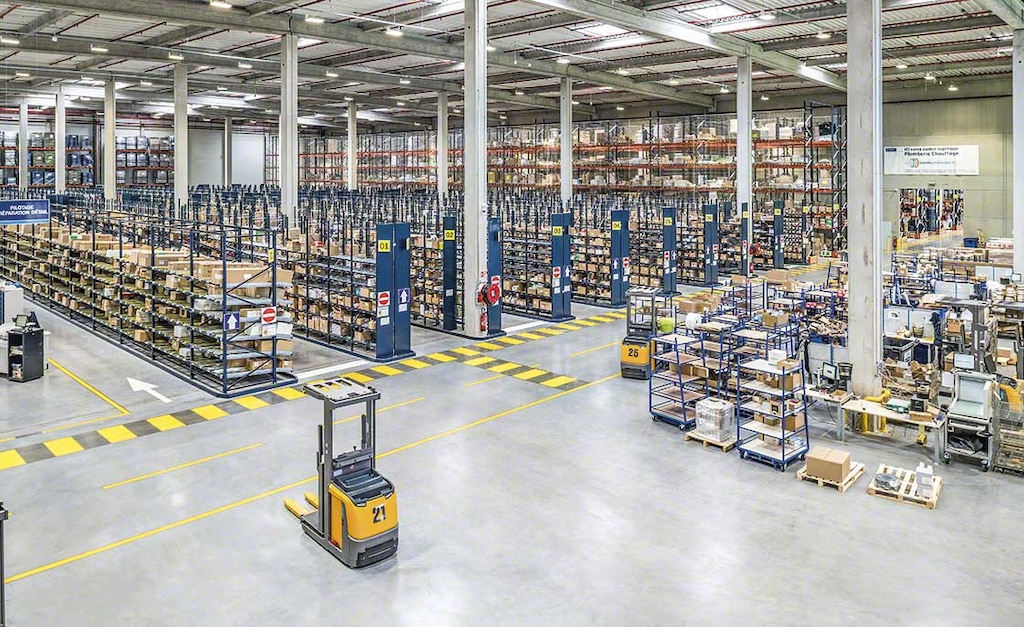
Relationship between production and logistics in industry
The task of manufacturing logistics is to reduce production lead times, that is, the time from the moment a work order is created until it becomes a finished product.
In fact, to cut manufacturing times, many industrial firms are turning to local materials and components suppliers. This trend has partially reversed the offshoring of companies; for example, Industry Week reports that production firms reshoring business to the US rose by 38% in 2018.
Another crucial factor in industrial logistics is stock management itself, which is fundamental for achieving faster production. To do this, the warehouse needs to be able to effectively manage the two types of demand affecting manufacturing logistics. The first is end-customer demand, whether based on sales forecasts or orders placed with the production center (this demand is independent of the manufacturing process). The second is factory demand, whereby all raw materials necessary to create the final product are requested from the warehouse (this demand depends on the production process).
Regarding the concept of factory demand, the manufacturing company is able to calculate with certainty which raw materials the production plant needs to make each product. Here, we should note the concepts of the BOM (bill of materials) and MRP (material requirement planning) systems. The BOM refers to the inventory or list of components required to manufacture the products, while the MRP system is the IT software that determines which materials are needed and in what quantity to produce a certain item.
Coordinating production and logistics areas involves, therefore, controlling these two types of demand (dependent on and independent of production process) and organizing industrial warehouses based on each kind. Storage installations linked to production plants can house finished products, parts, or raw materials that supply the manufacturing process or provide components or spare parts for after sales service.
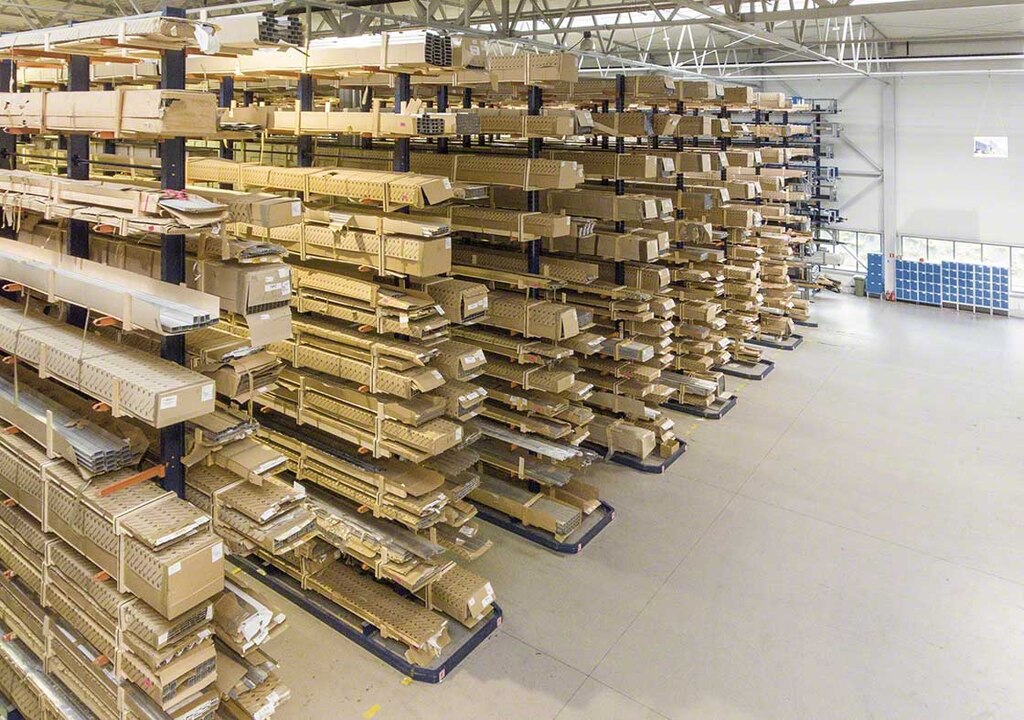
Maximizing warehouses devoted to industrial logistics
Applying a Lean logistics approach premised on the Lean manufacturing philosophy, efficient manufacturing logistics is built upon reducing operations that don’t add value to the product. Examples of this are internal transportation, lines or wait times between processes, and stock of work underway, among other factors.
The final aim is to provide improved service and drive down costs in general. So, then, how can you do this?
- Customized automation of the manufacturing process
When installations serve as depots for stock arriving directly from production, they need to be prepared to accommodate and move large amounts of goods, mostly pallets. The automation of materials transportation is a common solution when it comes to repetitive processes and heavy loads. Plus, it leverages space and improves warehouse productivity by drastically reducing goods handling incidents.
Nevertheless, there are also installations for components and spare parts devoted to manufacturing logistics whose operations are centered on the preparation of orders that supply the production lines. These warehouses usually have extremely diverse inventories and very small unit loads. As a result, one of the most common strategies consists of zoning the installation in line with the ABC analysis for inventory classification and automating material movements with roller conveyors to connect the various areas.
- Software for managing industrial logistics processes
WMSs for manufacturing add functionalities specially designed to enhance production to the core features of warehouse management systems. These programs, which, in some respects, work like MRP systems, control and coordinate the relationship between customer demand and demand determined by the manufacturing process.
Warehouse management systems have proven to be an essential tool for providing an overall view of inventory linked to production tasks. Having a WMS specialized in manufacturing facilitates:
- Classification by stock type: in manufacturing logistics, these can be raw materials, stock for works in progress or semi-finished goods, or finished products.
- Real-time stock visualization: the software ensures that you’re able to know the exact amount and condition of the goods at all time.
- Production according to the just-in-time method: this method would be impossible to apply without automated warehouse management.
Manufacturing logistics: the importance of integration
Nowadays, the industry finds itself up against a flexible and diversified manufacturing landscape in which, to provide efficient customer service, all the gears of manufacturing logistics need to fit together perfectly. In view of this paradigm, automation and the implementation of WMSs specialized in production processes are two key strategies for optimizing industrial logistics. To learn more about how to streamline manufacturing logistics at your warehouse, don’t hesitate to get in touch. One of our experts will analyze your warehouse operations and propose improvements.