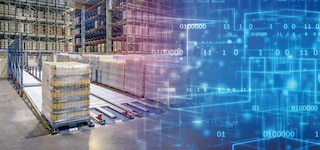
Smart packaging: the packaging provides the product info
Smart packaging differs from conventional packaging in that it monitors and communicates the condition of the products without having to resort to estimated expiration dates. It’s very practical in the case of food, drugs, and hazardous goods.
In the future, this packaging could form part of the Industrial Internet of Things (IIoT) by connecting to the web to share data on product conditions via sensors and software.
In this post, we’ll tell you all about smart packaging and how it works, in addition to the ways in which the supply chain can benefit from having real-time information on the status of the goods.
Smart packaging and why it’s important
Smart packaging (also known as intelligent packaging) refers to recipients capable of controlling the condition and quality of products during storage and transportation. It’s an evolution of traditional packaging that detects and records changes in a product’s environment. Smart packaging could prove to be a major advance for industry, particularly for the food sector.
According to the FAO, the UN organization dedicated to food and agriculture, the global volume of food waste is estimated at 1.75 billion tons a year, equivalent to a third of global food production.
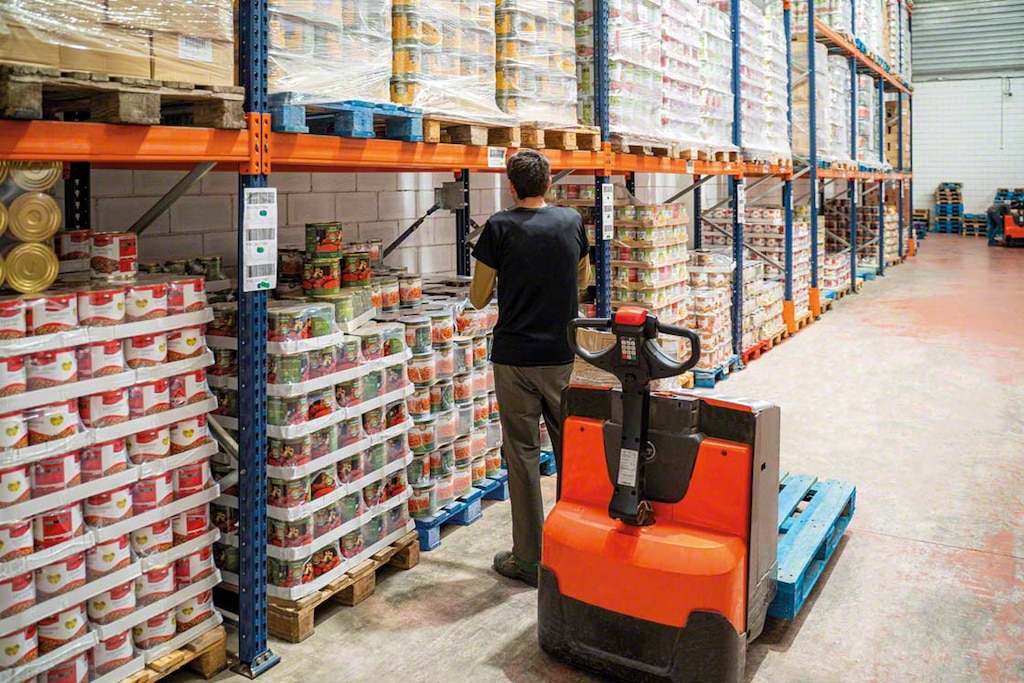
This situation is the result, among other reasons, of inefficient packaging. Therefore, food sector companies have a vested interest in developing solutions that minimize this waste, such as smart packaging.
Smart packaging incorporates sensors that detect bacterial growth, temperature changes, and gas composition that affect the condition of the foodstuff. Intelligent packaging is also capable of communicating these changes through visual indicators. This would result in fewer cases of food poisoning and less food waste.
Differences between traditional, active, and smart packaging
Despite the undeniable advantages of smart packaging, the biggest challenge now is to figure out how to manufacture them at a low cost and with a low environmental impact.
Before getting down to the nitty gritty, let’s differentiate smart packaging from other types of packaging:
- Traditional packaging. These recipients perform the basic function of protecting food from their external environment and preventing their degradation caused by environmental conditions such as light, humidity, dust, dirt, and other contaminants. They also make it easier to handle and move products.
- Active packaging. Unlike traditional recipients, these packages interact with the food to prolong its shelf life. They can incorporate additives inside them (in an envelope or on a label) that are released at the appropriate time. An example of active packaging would be a moisture absorber in a package of cookies to keep them fresh for longer while preventing the spread of bacteria.
- Smart packaging. This not only fulfills the functions of traditional packaging, but also provides consumers with useful information on the condition of the product. Thus, it ensures the quality and safety of its contents.
- Active and smart packaging. This combination of the two types above intervenes in the preservation of the product and, in addition, reports on its condition.
A look at smart packaging
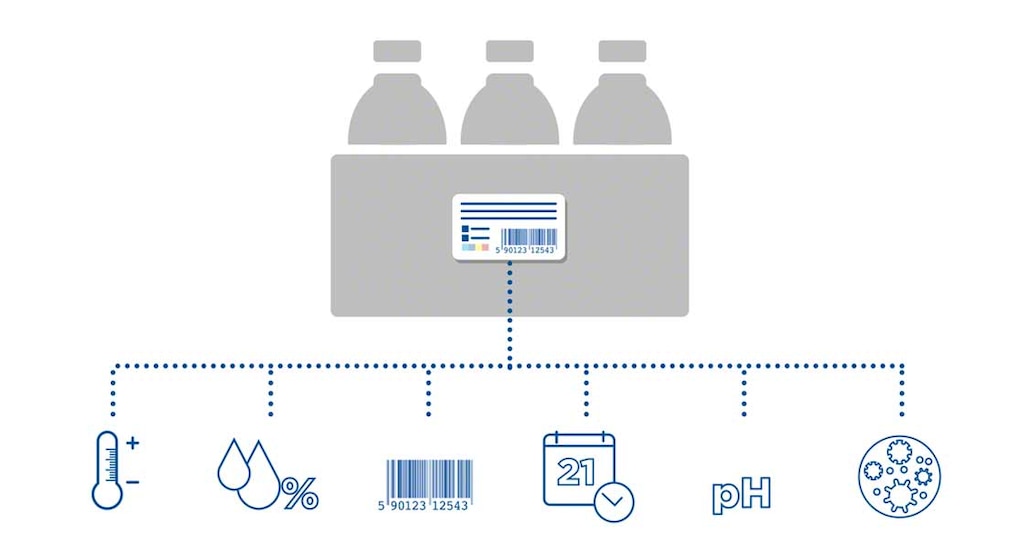
Intelligent packaging must be equipped with technology that controls the condition of the foodstuffs as well as with indicators that inform consumers. Let’s examine the devices these packages incorporate to carry out these functions:
Sensors
Affixed to the package, they serve to control the temperature, product conservation time, humidity, and freshness. There are different types of sensors that capture parameters such as pH and the presence of oxygen and carbon dioxide. This is reflected, for example, in sensors that register the ethylene given off by fruit in order to know how ripe it is.
Data indicators
Intelligent packaging can provide visual information on the condition of food. This is usually done by means of a transducer that converts the chemical signal into an optical one. An example of smart packaging that implements this system would be a package with a label that turns red to let the consumer know that the food has gone bad and shouldn’t be eaten.
Data carriers
Just like traditional packages, smart packaging should also facilitate management of the goods throughout the supply chain. For this purpose, these recipients are usually labeled with barcodes, QR codes, or RFID tags that supply basic information on the product type, SKU, price, and packaging and expiration dates. These labels — which are especially useful for controlling product traceability — also provide data on the proper way to store and distribute the products.
Smart packaging trends
Intelligent packaging is undergoing a continuous expansion, mainly in the US, Australia, and Japan. Manufacturers of these systems are developing new solutions with different types of indicators that bode well for food monitoring:
- Time/temperature. These indicators control the temperature and shelf life of packaged food. Consequently, it’s possible to know whether a food product has been exposed to inadequate storage conditions (which is very practical in cold storage warehouses).
- Freshness. These solutions detect the food spoilage or lack of freshness. To do this, they perceive volatile metabolites such as carbon dioxide or ammonia that are naturally released when a food’s intake conditions are no longer optimal.
- Leakage. These indicators react to the presence or absence of gases such as oxygen and carbon dioxide, used to monitor food quality.
- Smart ink. Another intelligent packaging trend comprises the incorporation of thermochromic ink to indicate the optimal product consumption temperature. It’s a good way, for example, to identify whether the product is too hot or too cold.
Smart packaging is expressly designed to facilitate the management of food products. In their warehouses, companies in this industry strictly monitor the goods to prevent food spoilage and the associated consumer risks.
To carry out rigorous control of the products, it’s essential to have a warehouse management system, such as Easy WMS from Interlake Mecalux. The software supervises entries and dispatches and ensures traceability. By adding smart packaging to this, control and management of the goods will be even more accurate, since the information it provides enables you to make better goods-management decisions and detect handling errors.
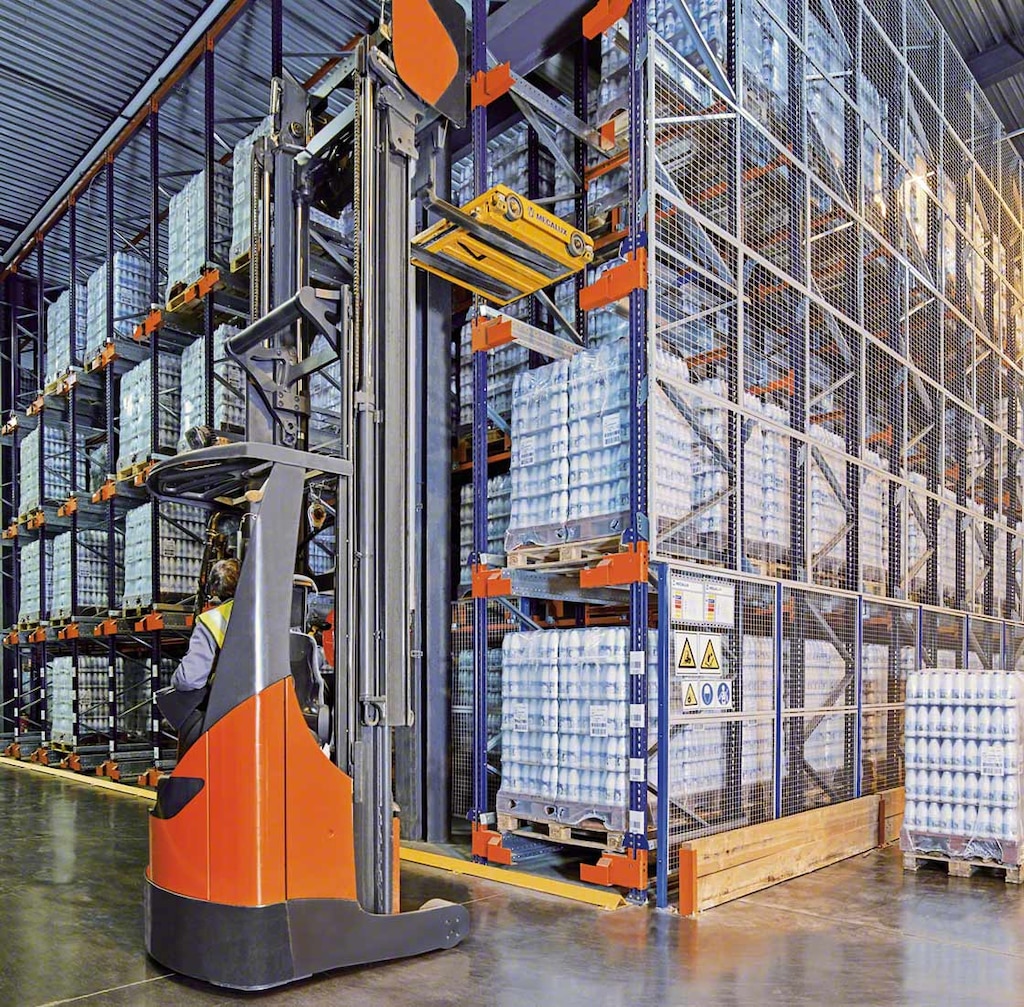
Combating food waste
Food companies have to be extremely demanding when it comes to the traceability of their products. To accomplish this, the first step is to outfit their logistics facilities with a warehouse management system that optimizes and orchestrates operations, in addition to making sure the cold chain remains intact.
Smart packaging improves goods management, as it has been specifically devised to minimize food waste, improve food safety, and ensure the utmost quality of these products. However, in spite of their undeniable advantages, their current cost is keeping them from becoming a widespread solution.
As this packaging becomes more popular, both businesses and consumers will benefit. Likewise, supply chain management will be much more streamlined and effective, since logistics managers will have all the information they need to ensure correct storage and shipping conditions.
If you think the time has come to optimize your logistics operations and more accurately control the goods in your warehouse, don’t hesitate to get in touch. We’ll advise you on which solutions will make the most of your facility.