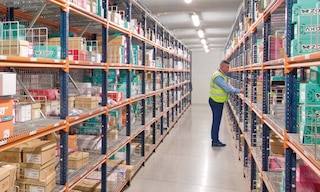
Warehouse order picking: Manual vs. automated
Warehouse order picking is one of the most crucial processes in logistics operations. Nevertheless, order fulfillment has evolved over the years, and today, there are new options for carrying it out.
What is manual order picking?
Manual picking is a fulfillment phase where associates travel through the warehouse to locate and collect products required for orders. The process — performed via the person-to-goods strategy — spans everything from order receipt to item picking and packing. Manual warehouse picking is the most traditional picking method and is still common in numerous facilities. However, technological advances enable companies to streamline how they carry out this activity.
Manual vs. automated picking
Both manual and automated picking can be performed using techniques such as discrete (order by order), wave, zone, or batch picking. Below are the main differences between these two kinds of warehouse order picking:
Manual | Automated |
---|---|
Indicated for warehouses with little capacity, few SKUs, and no plans to expand. | Easily scalable systems suitable for companies looking to expand their activity. |
Flexible: allows hiring new associates to pick orders during peak workloads. | High-capacity solution with automatic picking tools to handle rises in demand. |
Picking is carried out during associate work shifts. | Automated systems can operate uninterruptedly. |
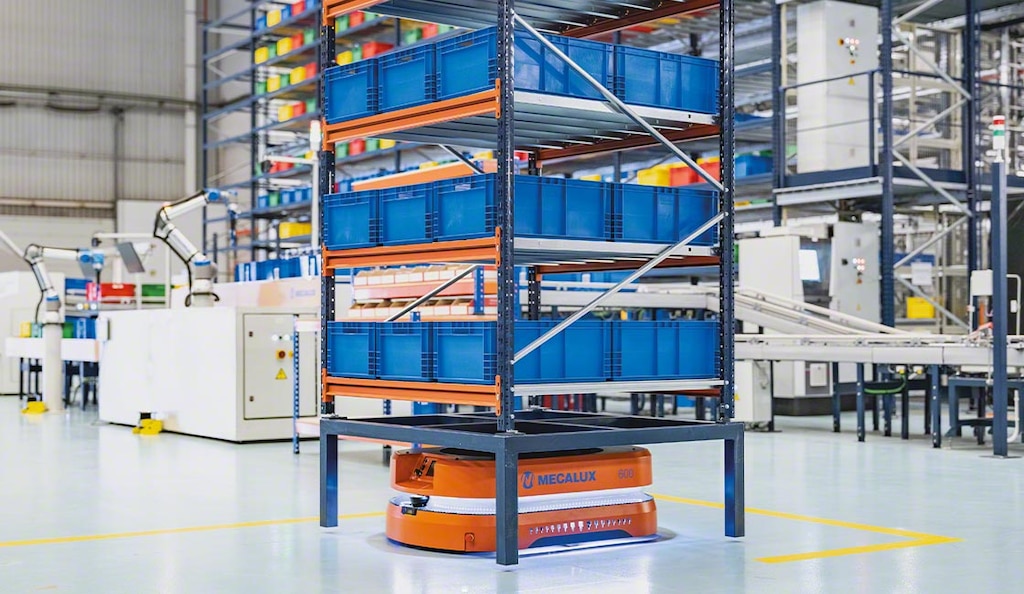
From manual to automated warehouse order picking
Selecting the warehouse order picking technique that best matches your facility is essential for efficient operations. You’ll also need to have an appropriate strategy to implement it effectively.
Pick-to-light
With pick-to-light (PTL) systems, warehouse pickers scan the picking location and retrieve the stipulated number of units. When they finish, they press a confirmation button to notify the warehouse management system (WMS). PTL systems are also helpful when filling new orders, as the locations to pick from light up automatically. This process is also compatible with pick-to-cart.
Voice picking
Voice-directed warehousing (also known as voice picking or pick by voice) is a system that guides operators in the picking process through audible commands. Receiving instructions on mobile devices or through headsets improves ergonomics and allows operators to work hands-free.
RF picking
In radiofrequency (RF) picking, associates use wireless terminals to receive commands from the warehouse management system. Software like Easy WMS shows these operators where items are located and how many they need to pick. Once they complete the task, they confirm it on their terminals to receive new instructions.
Tote-to-person
Tote-to-person is more automated than the alternatives mentioned so far. This system delivers small totes, boxes, or bins directly to associates without their intervention, through solutions like mini-load storage and retrieval systems (AS/RSs).
Shelf-to-person
Similar to tote-to-person, with the shelf-to-person method, entire shelving units are moved to employees automatically. To do this, companies use autonomous mobile robots (AMRs), automated vehicles capable of safely navigating warehouses. This saves associates from walking around the facility to locate the products required to fill orders.
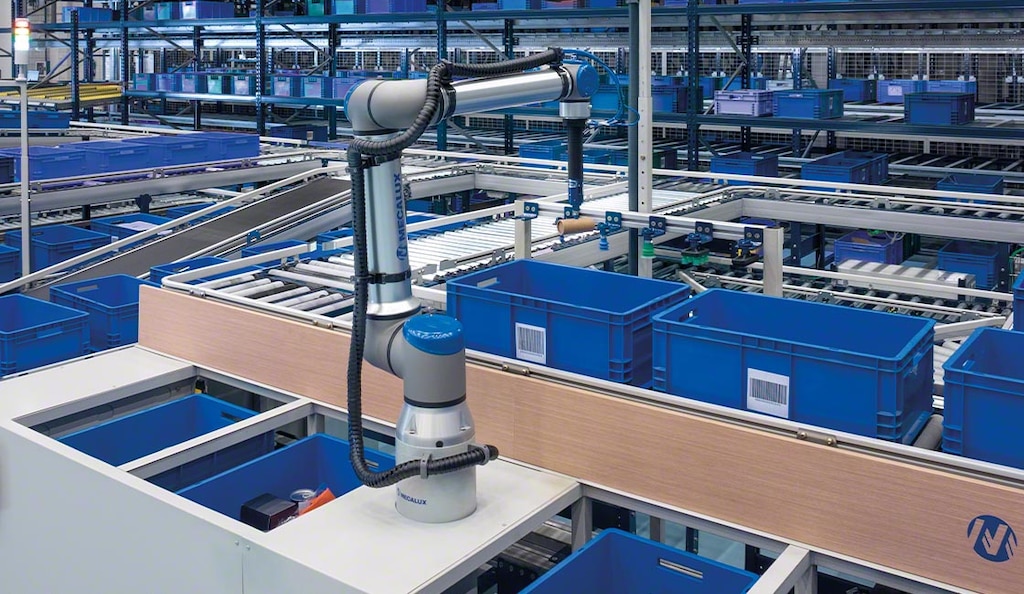
How can you automate manual picking?
In warehouse order picking, there are various ways to swap manual options for automated ones. In addition to those mentioned above, other alternatives include:
- Picking robots. This is the ideal solution for facilities with high activity levels. These robots automate order picking by retrieving products from storage totes and placing them in order totes. Equipped with versatile gripping devices, they incorporate computer vision software powered by deep-learning algorithms.
- Mini-load systems. Warehouses that leverage automated handling and internal transport systems for boxes are more efficient than manual facilities.
- Accumulation conveyors. Made up of rollers or chains, these systems transport, distribute, or accumulate goods at the positions required by warehouse associates. They can handle pallets and boxes, making them perfect for optimizing repetitive workflows.
How to reduce warehouse order picking errors
Whether you opt for manual, automated, or semi-automated picking, warehouse management software is a great ally. It coordinates available inventory, identifies products needed to fulfill orders, and anticipates incoming goods.
- A solution like Easy WMS receives information on orders pending fulfillment and shares it with associates and automated systems alike.
- It manages available locations and ensures product traceability at all times.
- The software optimizes pick paths to avoid unnecessary warehouse travel.
- It monitors the fulfillment process, tracking picked items and processing times.
Automate warehouse order picking with Interlake Mecalux
The Mecalux Group’s extensive experience designing and installing racking systems dates back to 1966. Be sure to contact Interlake Mecalux for expert advice on intralogistics automation, internal transport, inventory management, and order fulfillment digitalization through software solutions.