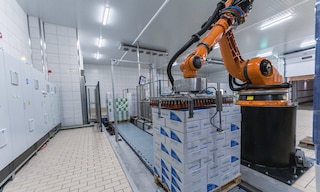
Warehouse robots: technology automates logistics
Warehouse robots are a solution that brings maximum productivity to logistics facilities. At a time when speed and efficiency have become essential for any warehouse, companies seek solutions that drive their logistics operations.
In this post, we examine the robots most widely used in warehouses — mainly automated guided vehicles (AGVs), autonomous mobile robots, robotic arms, and automated storage and retrieval systems (AS/RS) — and analyze their applications and advantages.
What’s a warehouse robot?
Warehouse robots are devices employed to automate flows of goods and increase productivity. These technologies work with full autonomy or in collaboration with operators to perform tasks such as moving products between two points, preparing orders, and storing products on racks.
With warehouse robotics, companies can serve their customers without interruption. Robots and automatic handling equipment perform operations in logistics facilities with minimal operator intervention.
In recent years, warehouse robots have had a huge impact on the supply chain and have been implemented in many facilities. The reason is obvious: companies turn to technology to boost the flexibility and throughput of their logistics operations. According to a study by consulting company Research and Markets, the global logistics robots market was valued at over $1.8 billion in 2020 and is slated to reach over $2.35 billion in 2026.
4 benefits of warehouse robots
Up against a constantly changing market, businesses look for automated solutions to ensure on-time order deliveries. Warehouse robots have proven an effective alternative for optimizing companies’ supply chains. Their advantages include:
1) Increased accuracy in operations. Manual management of goods entails a high risk of errors (for example, putting an item in the wrong location or preparing an order without the corresponding product). Robots work in logistics facilities with full autonomy. By following instructions from the warehouse management system (WMS), they’re extremely precise and don’t make mistakes.
2) Enhanced productivity and efficiency. Implementing robots in the warehouse makes work much faster and more efficient. For example, operators can remain at their pick stations while the stacker cranes and conveyors automatically bring them the goods they need to prepare orders. This saves them from having to walk around the warehouse to locate the items they require.
3) Improved safety. Goods handling involves a greater risk of accidents, especially if the loads are heavy or managed from uncomfortable positions and using repetitive movements. Robots carry out various tasks accurately, eliminating the likelihood of accidents.
4) Collaboration with operators. Robots simplify routine operator tasks and help them to be more efficient. For example, these machines can effortlessly move large load volumes, allowing operators to focus on other higher value work.
In short, automating warehouse processes through robots is one of the most effective strategies for meeting the threefold objective of cutting operational costs, improving service quality, and maximizing the overall effectiveness of the logistics facility.
Types of warehouse robots
Robotics is a constantly evolving technology that incorporates more and more improvements to implement new functionalities. These are some of the robots most commonly found in warehouses:
AGVs
Automatic guided vehicles (AGVs) have expanded on the market over the last few decades. These transportation machines are similar to forklifts but are driverless and move around the warehouse following a preset route. They are tasked with moving goods between two points in the building with full autonomy, freeing operators from this tedious work.
AGVs can connect different parts of the facility or link the storage area with the production lines. The latter is the case of multinational pharmaceutical and biotech company Novartis, whose automated rack-supported warehouse built by our company in Poland is directly connected to its production center by means of AGVs. “The use of these forklifts lets us completely free up space and gangways,” says Tomasz Marchewa, Supply Chain Manager at Novartis.
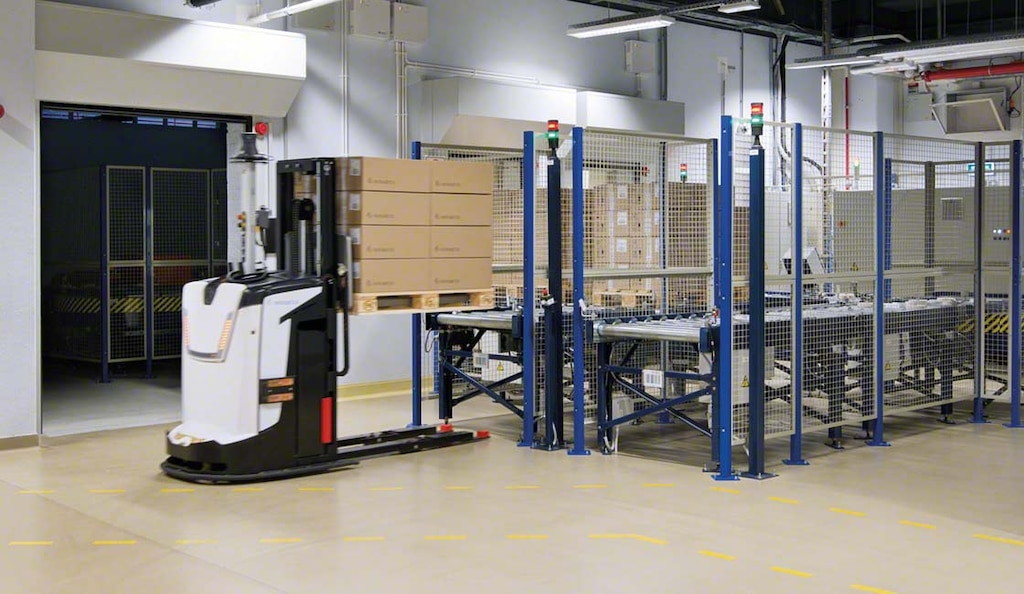
Autonomous mobile robots
With the help of technology such as AI and machine learning, autonomous mobile robots (AMRs) are devices capable of performing tasks and moving around the warehouse without the need for anyone to direct them. To that end, they are equipped with sensors, software to guide them, and digital layouts of the warehouse to interpret their environment.
Their function is the same as that of AGVs: to move product between two points. The difference between the two lies in the navigation systems they use. While AGVs travel along a predefined route with laser- or wire-guided systems, AMRs adapt their routes according to the information they receive from their environment in real time.
Spanish emergency lighting company Normagrup has a miniload system (AS/RS for boxes) set up by our company that’s linked to the production lines via four AMRs. Each time a kit is assembled, an AMR picks it up and brings it to the production line that requires it as quickly as possible.
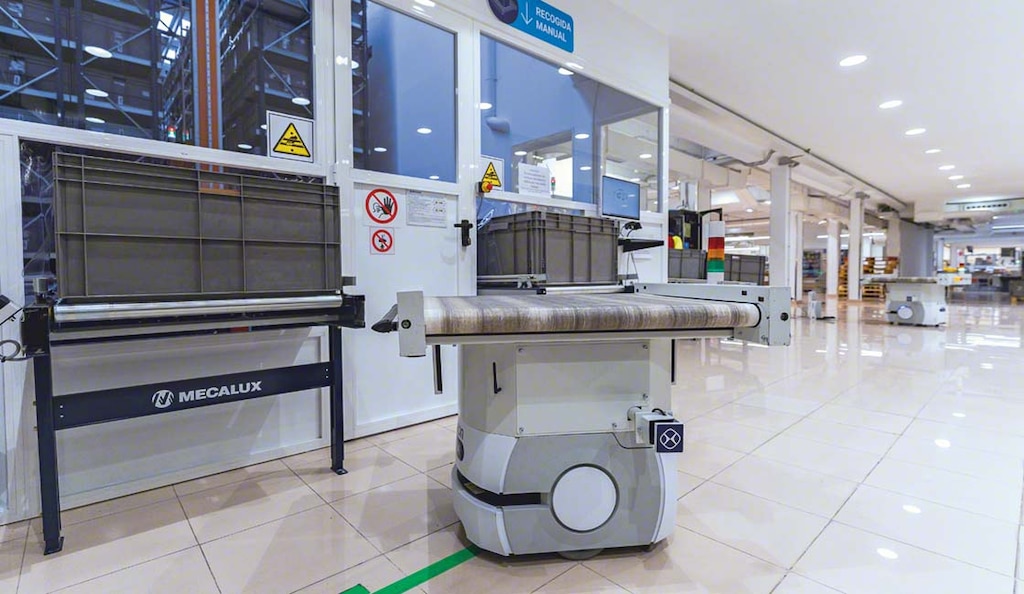
Automated storage and retrieval systems (AS/RS)
Automated storage and retrieval systems (AS/RS) enable companies to implement robotics in their logistics operations. Automated storage equipment such as stacker cranes for pallets, miniload systems, and the automated Pallet Shuttle system are responsible for storing the goods in their corresponding locations with complete autonomy.
Meanwhile, automatic transportation equipment, such as pallet conveyor systems, brings the goods anywhere they are needed. The use of these machines brings a major advantage: operators can concentrate on other tasks that add more value.
Automatic handling equipment can work 24/7, allowing goods to be moved continuously. Intersurgical, a manufacturer of medical equipment for respiratory support, has a warehouse built by our company in Lithuania with completely automated operations to cope with the high production rate resulting from the COVID-19 pandemic. Thanks to automation, the business was able to serve its customers without delay and distribute all its medical devices to hundreds of hospitals and healthcare centers.
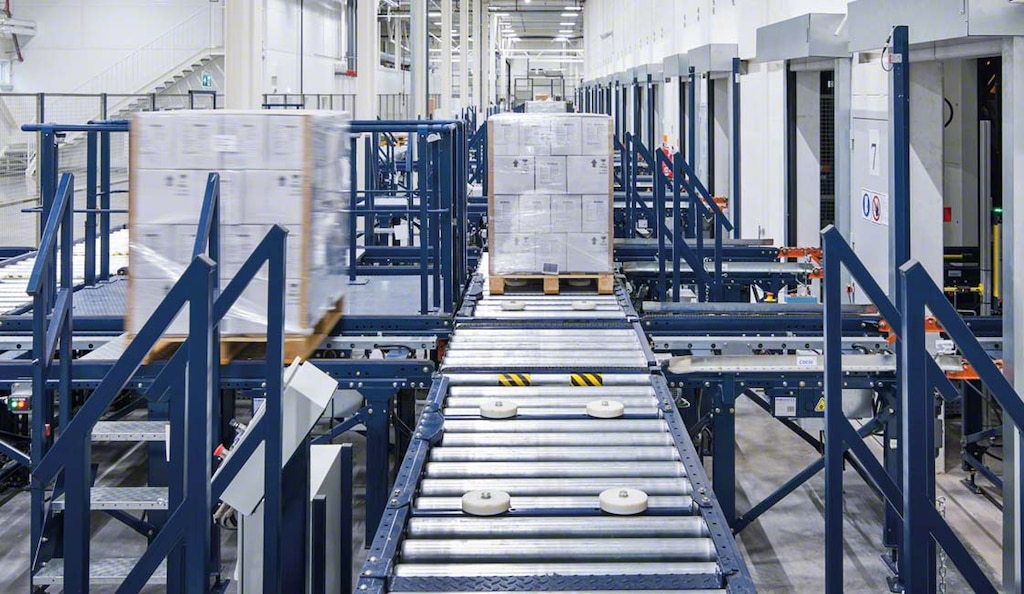
Robotic arms
The use of robotic arms in warehouses is also on the rise, as they facilitate order preparation and help operators to manage heavy loads. These robots are similar to human arms, as they contain components that carry out rotational motion and linear displacement.
These arms can operate completely independently (for example, pick and place robots, which are outfitted with an artificial vision system) or can work together with operators. The latter describes the case of Venis, the ceramic floor and wall tile manufacturer belonging to the Porcelanosa Group, which has an automated warehouse built by our company with a large area allocated to order picking. Since the business manages very heavy items, the pick stations are equipped with robotic arms that lift the heavy packages with minimal operator effort.
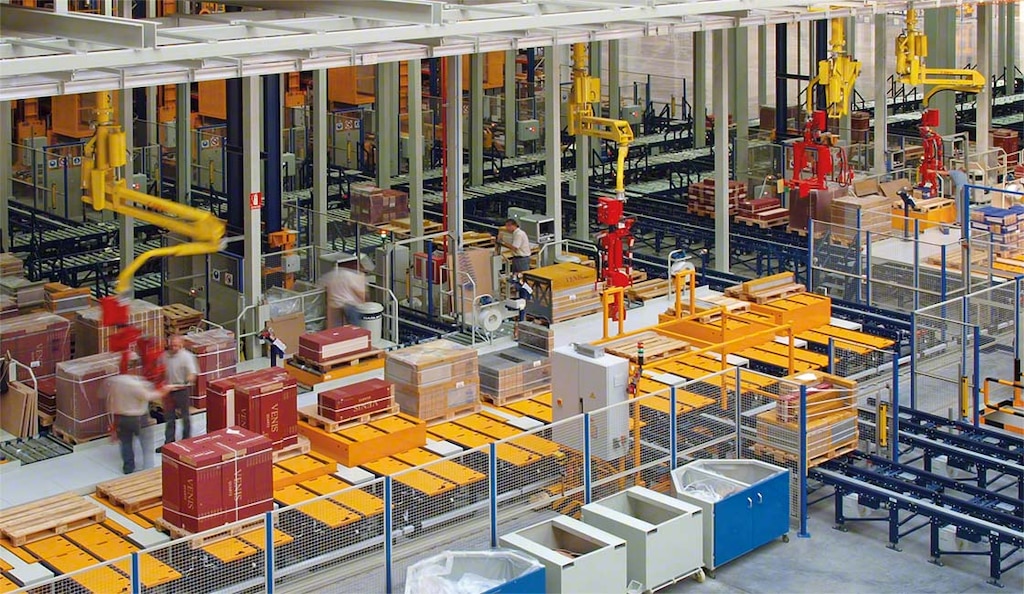
Alliance between warehouse robots and software
Warehouse robots are coordinated by means of a warehouse management system (WMS) that guides them in all movements to be carried out. In fact, in high-tech warehouses — in which handling equipment and robots perform operations such as goods movements and order preparation — implementing a WMS is a must.
A warehouse management system such as Easy WMS from Interlake Mecalux can organize operations in the facility and send the robots instructions on how to carry them out effectively. The software also monitors all product movements to know their location in real time and eliminate errors by up to 99%.
Automation for logistics in expansion mode
Warehouse robots are a smart solution for adapting to the changes in the supply chain. The incorporation of technology in logistics installations is an investment designed to improve results and stimulate business growth.
Against this backdrop, more and more companies are resorting to automation to speed up their storage and order prep tasks. At Interlake Mecalux, we have extensive experience in implementing these types of solutions for businesses in all sectors. Be sure to get in touch. We’d be happy to show you how robotics can raise the throughput of your warehouse.