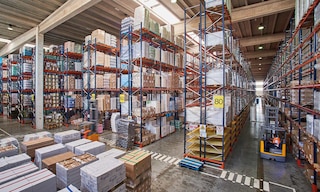
Warehouse storage techniques for efficient use of space
Warehouse storage techniques comprise methods for organizing goods in a logistics facility. Depending on their particular characteristics and demand level, items can be placed on the floor or on racking. Once the company designates the place in which the products will be housed, it defines criteria for storing them: e.g., grouping similar products in the same area or allocating the lower levels of the racks to heavy products.
Choosing the right warehouse storage technique is a vital decision for each logistics facility; that is, the option you decide on will directly impact the way in which warehouse operations are run. To assess which method best meets the needs of the business, it’s essential to analyze variables such as the available space, type and quantity of items stored, packaging used, and workflows.
In this post, we take a look at the most common warehouse storage techniques in logistics facilities:
Floor storage
Also known as block stacking, floor storage is a warehouse storage technique whereby goods are placed directly on the floor. High-turnover items housed on the floor are normally grouped in a specific warehouse zone to make them easier to locate in order picking.
One of the advantages of floor storage is cost savings. This warehouse storage technique is the most cost-effective of all, as it doesn’t require racks. However, this option is generally ruled out because of its drawbacks: it requires operators to travel long distances to locate SKUs when preparing orders or replenishing inventory, it squanders the available surface area, and it entails a high risk of collapse.
Pallet rack storage
Pallet racking is the most widespread warehouse storage technique. These structures optimize space in the facility, ensure that the operators and the goods are safer and more secure, and maximize warehouse throughput.
Pallet racking can be broken down into three categories:
Pallet rack storage with direct access
With pallet racks with direct access, products can be directly removed from the working aisles. This solution provides total accessibility to all goods, facilitating storage and order prep tasks. These type of racks require wide aisles so that operators can insert and retrieve products from their locations with the help of forklifts.
This group primarily comprises two storage systems:
- Pallet racks. This is one of the most popular systems seen in warehouses due to its versatility, low cost, and easy implementation. Pallet racks can be single- or double-deep (placing one pallet behind the other in each slot). Operators can work with these racks using any type of handling equipment, as long as the aisle is wide enough.
- Mobile racking systems. These consist of pallet racks installed on mobile bases that move automatically to open a working aisle. When the operator issues the command to open an aisle via radio control, the aisles cascade open, allowing workers to enter an aisle and deposit or remove the goods in their locations. This system minimizes the number of aisles, generating more storage capacity without forfeiting direct access to the goods.
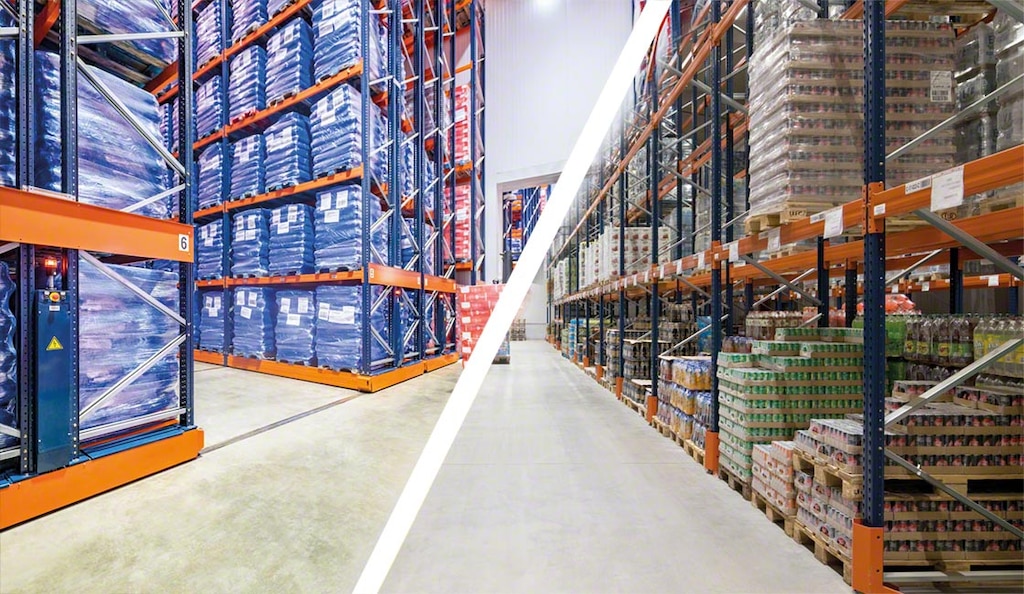
High-density pallet rack storage
Compact or high-density pallet rack systems are a warehouse storage technique whereby the aisles in which the handling equipment operates are reduced. The racks provide greater storage capacity and make better use of the warehouse surface area compared to racking with direct access. Compact storage is a go-to option for storing consumer products with many pallets and few SKUs.
This category includes:
- Drive-in drive-thru pallet racks. With these racks, operators must enter the structure with their handling equipment to deposit or remove the pallets. These racks are made up of lanes with rails on which the pallets are placed.
- Push back racking systems. The levels of these racks are formed by slightly inclined, free-rolling carts or carriages. Their operation is quite simple: as a pallet is loaded, it pushes the ones already stored towards the back. Meanwhile, when a pallet is removed, gravity moves the ones stored behind it forward.
- Pallet flow racks. With these types of racks, made up of slightly sloped lanes with rollers, pallets move automatically from the highest part of the lane to the lowest. This warehouse storage technique guarantees optimal product turnover, since the first pallet to enter the lane will be the first pallet out.
- Pallet Shuttle. This evolved version of high-density racking incorporates a motorized shuttle that handles the pallets inside the storage channels. This motor-driven shuttle speeds up storage tasks significantly.
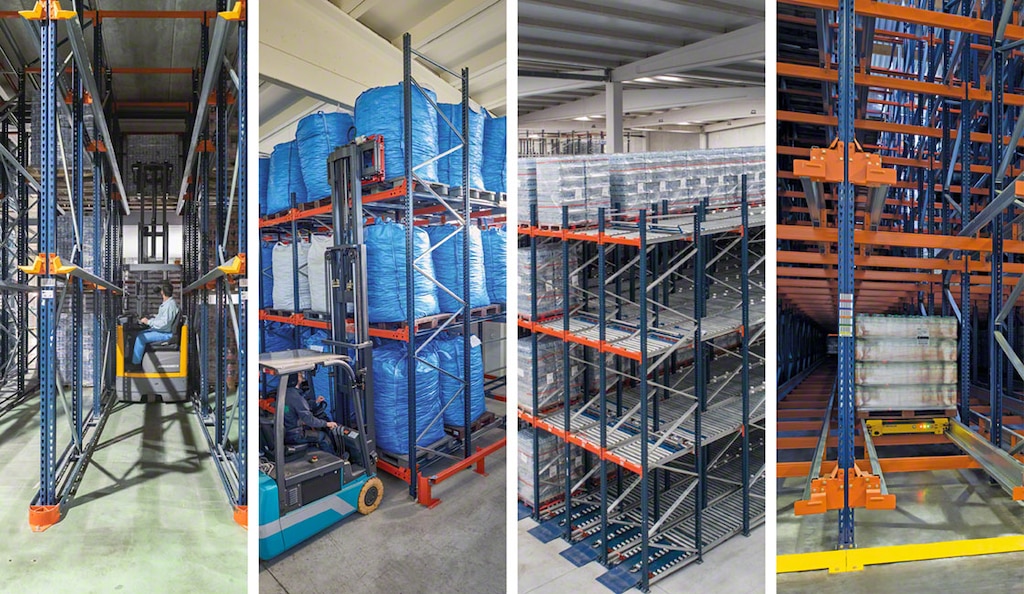
Storage of special or bulky products
Special goods and long/large items (tires, long pipes, profiles, reels, etc.) require particular warehouse storage techniques. For these cases, companies usually rely on two kinds of racking:
- Cantilever racks. These racks comprise load-bearing arms anchored to columns. The arms hold bulky products of variable lengths, such as pipes or profiles. One of the particular features of these racks is the direct access they offer, facilitating goods handling.
- Racking for reels and drums. This consists of pallet racking accessories designed to store and facilitate the handling of products wound on reels (e.g., cables and electric wires) and cylindrical loads. These accessories can be easily adapted to the characteristics of the goods as well as their size and use.
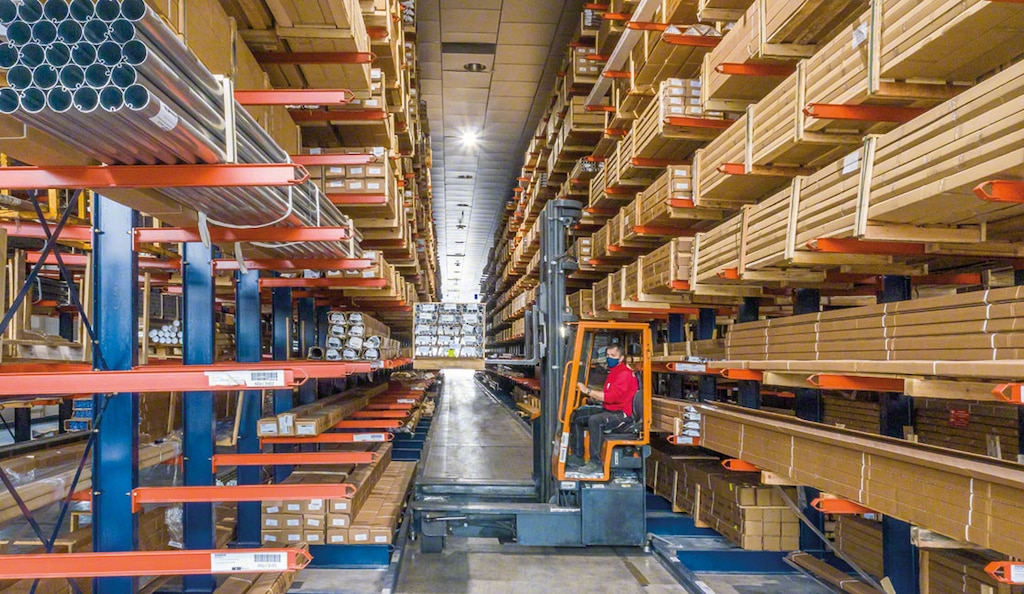
To choose the ideal warehouse storage technique, companies should analyze the characteristics of their goods, the space available to them, and the flows in their facilities. With all these data, storage system suppliers can advise them on whether their best bet would be solutions with direct access, high-density storage, or racking for special bulky goods.
Optimal location management
In addition to applying the correct warehouse storage technique in terms of systems, it’s also important to determine the proper way to slot the goods according to the available space.
Good management of products and tasks in the facility increases physical storage capacity and improves productivity. To this end, many companies invest in a warehouse management system (such as Easy WMS from Interlake Mecalux). A WMS automatically assigns each good an optimal location based on several variables such as item type, SKU, and turnover.
Automatic movement of goods
Another warehouse storage technique employed by more and more businesses comprises automated storage & retrieval systems (AS/RS). These solutions outfit warehouses with automatic handling equipment, e.g., stacker cranes (AS/RS for pallets) and pallet conveyor systems, which move the goods with total autonomy.
Automation is extremely useful for increasing speed in goods inflows and outflows. It also limits cost overruns in the facility, such as those caused by errors in storage and order prep tasks.
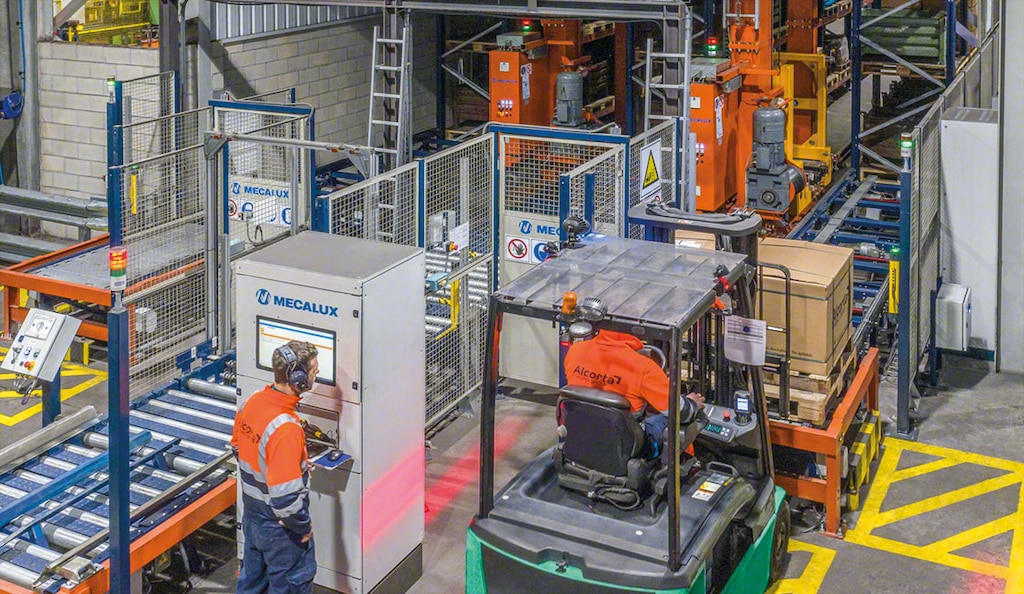
Warehouse storage techniques for an orderly facility
Organization is crucial in any warehouse. For this reason, companies look for the ideal warehouse storage techniques to house all their products effectively and facilitate operations, from goods receipt to order preparation and dispatch. Choosing a storage system is a major decision for any business — it has a direct impact on the warehouse’s throughput. Therefore, it’s a good idea to rely on the advice of a storage solutions expert.
At Interlake Mecalux, we have vast experience in providing storage solutions to meet any logistics need.We have an extensive catalog of storage solutions, from standard pallet racking to fully automated systems. Be sure to contact our technical team to find out which solution is best for your warehouse.