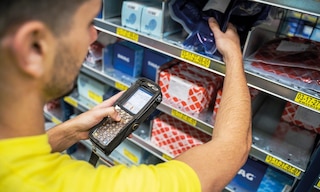
Discrete picking: Definition and best practices
Discrete order picking is one of the most widely used order preparation methods due to its simplicity. While it’s ideal for small-scale operations and warehouses with low product turnover, its implementation and benefits depend on each company’s logistics needs.
What is discrete picking?
Discrete picking — also known as single-order picking or piece picking — is an order fulfillment method where a warehouse associate collects all the items required to complete an individual order before moving on to the next one. This person-to-goods approach is the simplest kind of picking, characterized by its sequential and organized workflow within the warehouse.
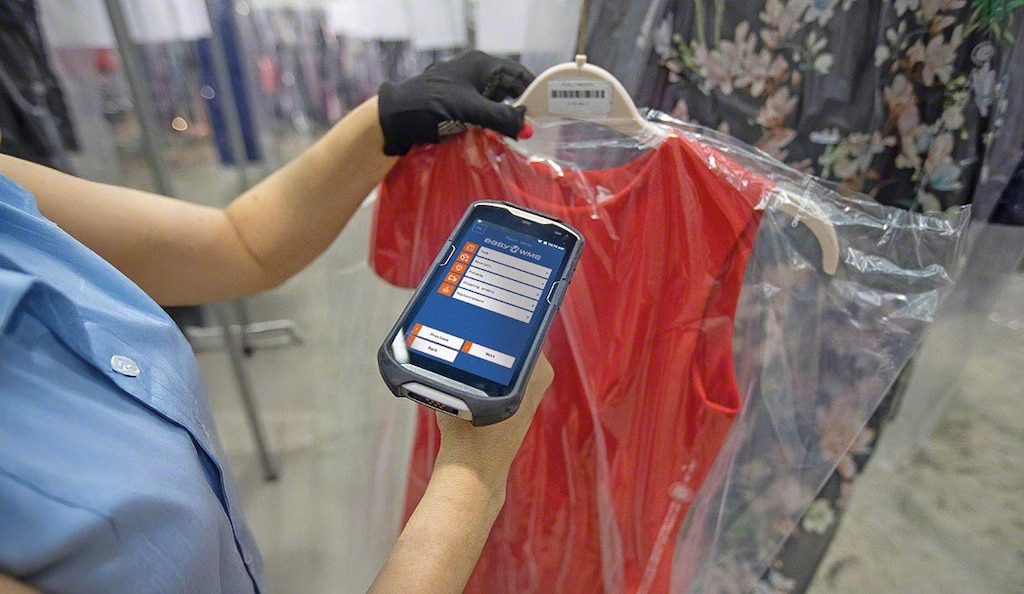
How is discrete picking performed in a warehouse?
These are the steps involved in carrying out discrete order picking:
- Order receipt. A warehouse management system — such as Interlake Mecalux’s Easy WMS — generates a pick list containing the items for the order. This list includes details such as product SKU numbers, required quantities, and storage locations.
- Route planning. The most efficient path through the warehouse is mapped out to collect the items. While discrete picking doesn’t optimize routes as effectively as other methods like batch picking or zone picking, proper planning can help minimize travel.
- Product picking. The associate moves through the facility, retrieving each item from its designated location. At this stage, verifying quantities is crucial to prevent errors.
- Order consolidation. Once all the items are gathered, they are checked to ensure they match the original order.
- Packing and shipping. The completed order is put in a box, labeled, and prepared for shipment to the customer.
Pros and cons of using discrete picking
This strategy is particularly useful in facilities with low order volumes. It offers the following benefits:
- Error reduction. Processing orders one at a time minimizes the risk of mixing up products, limiting picking errors.
- Simplified management. This method is easy to implement and doesn’t require complex staff organization.
- Ideal for order personalization. This type of picking is recommended when orders vary significantly in content and quantity, as it allows for greater flexibility and accuracy.
Despite its advantages, discrete order picking also presents these drawbacks in the warehouse:
- Lower productivity. Since only one order is picked at a time, processing capacity is limited compared to other order fulfillment methods.
- Higher costs. Excessive travel and idle time can lead to inefficiency and drive up costs, particularly in large facilities where movement is more extensive.
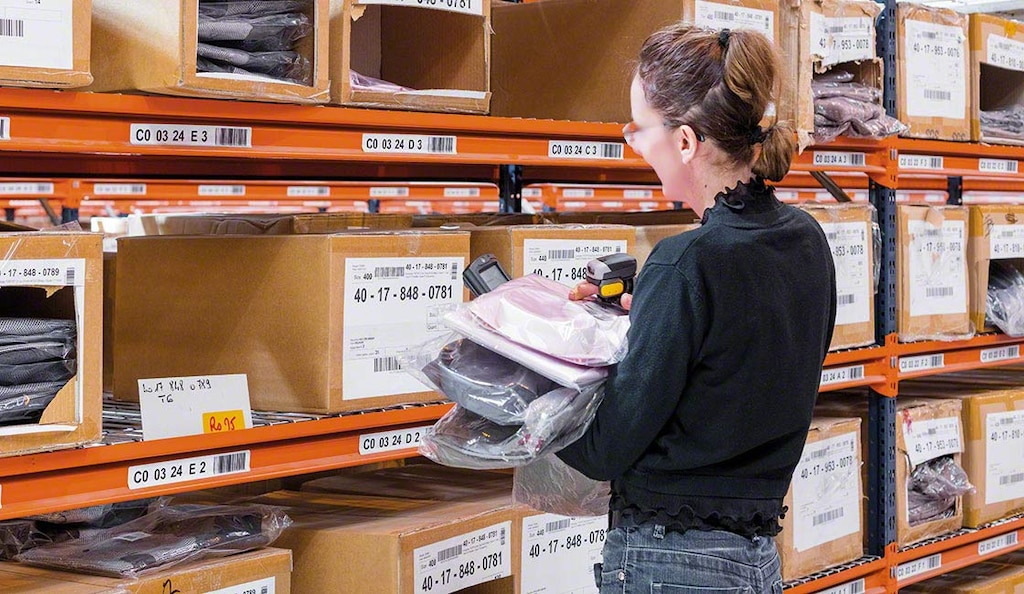
Real examples of discrete order picking
Single-order picking is an effective solution in small-to-medium-sized warehouses and those that prioritize reliability over speed.
For instance, in the facility of decorative paint manufacturer Pinturas Lepanto, orders are filled individually, one after another. To maximize efficiency, the company uses Easy WMS. The software guides associates to the correct location and tells them which items to retrieve from the pallet racking. When preparing orders, Easy WMS factors in the products’ weight and size. Associates first pick the heaviest barrels of paint and then place the smaller cans on top. “Thanks to the control and instructions from Easy WMS, we never ship incomplete or incorrect orders,” says José Ignacio Ruiz, Warehouse Manager at Pinturas Lepanto in Binéfar (Spain).
In France, electrical and DIY product retailer Unipro Group fulfills and ships up to 400 orders with more than 2,200 lines in its two facilities with the help of Easy WMS. Orders with a large number of items are processed individually. Associates pick the items from the racks and transport them directly to the consolidation and shipping area for customer distribution. “Properly organizing operations with the Mecalux software has boosted our productivity,” says Julien Exbrayat, Logistics Manager at Unipro Group.
Digitalization: Invaluable for discrete picking
Digitalization plays a vital role in optimizing discrete order picking. Warehouse management systems like Easy WMS make it possible to improve order fulfillment accuracy, reduce errors, and minimize idle time. Additionally, integrating technology enables the use of RF scanners and picking assistance systems (e.g., pick-to-light and voice picking), which increase productivity during the process.
Picking is essential for maximizing supply chain efficiency. If you’re still managing this process manually and want to optimize performance, it’s time to move toward digitalization. Contact us to discover how a WMS can take order fulfillment to the next level.