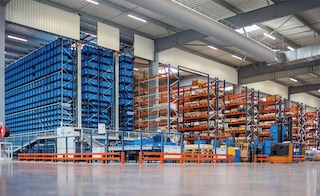
Storage systems: which one is right for your warehouse?
There are various ways to store products in a facility, from stacking pallets directly on the floor (block stacking) to placing them in storage systems. The latter method is the most common as well as efficient, since depositing goods on racks optimizes warehouse space and, at the same time, maximizes operational productivity.
In a facility in which multiple products are managed, ideally, each one should be stored in the right system. So, at this point, you’re probably asking yourself: which storage system should I install? The choice depends on variables such as the goods’ characteristics, size, and turnover.
In this post, we’ll examine the various storage systems for palletized goods typically found in warehouses, in addition to their advantages and applications. In the case of handling goods in boxes or containers, you should opt for boltless shelving or miniload systems (AS/RS for boxes), which we’ll touch on at the end of this article.
What’s a storage system?
Let’s begin with the definition of a storage system: it’s a set of physical structures designed to store goods optimally while prioritizing the effective use of space, ease of access, and the organization of the products according to certain criteria.
It’s standard to employ industrial racks: structures that are fixed to the warehouse floor and made up of locations in which the goods are placed. We can differentiate between two categories of racking: with direct access or compact storage. The first, as its name indicates, provides full accessibility to the products, facilitating storage and order picking tasks. The second, on the other hand, optimizes space in order to accommodate a larger number of products.
Choosing between a system with direct access and a compact one will depend on factors such as the number of SKUs, number of units of each one, and consumption criteria. Based on the company’s needs the balance will tip to one side or the other.
Below, we’ll take a look at the particular features and storage solutions comprising these two groups.
Racks with direct access
Solutions with direct access are noted for making the goods directly accessible from the working aisles. This ensures that products are removed very quickly, at the cost of losing storage capacity. This category includes:
Pallet racks (single- and double-deep)
Pallet racks are commonly seen in facilities that manage many SKUs and few pallets per SKU and in warehouses with a high volume of goods movements. They’re recommended for small or medium-sized facilities and those that store bulky products.
One of the particular attributes of these racks is their ability to adapt to any unit load, weight, and volume. Therefore, logistics providers usually resort to them to store very diverse products and pallets of different sizes and characteristics. Plus, picking can be done directly on the first pallet level.
Case studies:
- The racks at the Delta Children facility in the US offer storage capacity for 30,606 pallets.
- Unilever’s warehouse in Brazil with single- and double-deep racks.
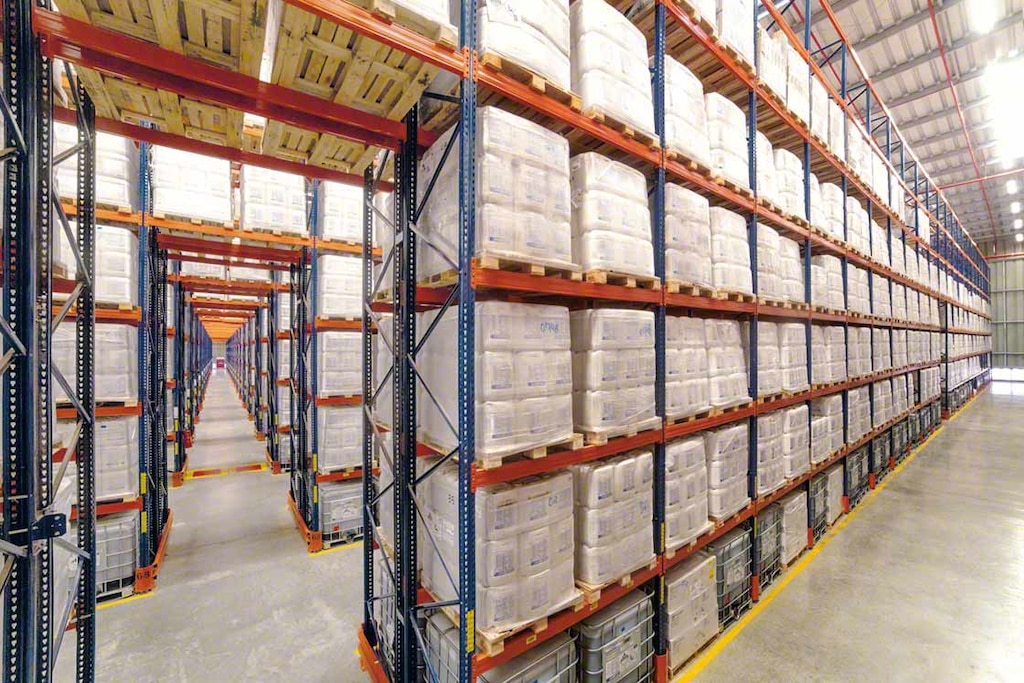
Mobile racking systems
These consist of racks installed on mobile bases that slide laterally and autonomously over rails in the floor. They incorporate motors and control devices to ensure their movement is smooth and safe.
Movirack mobile racking minimizes the number of aisles to house a larger number of pallets in a specific, limited space without forfeiting direct access to the products.
Although they’re apt for facilities operating at any temperature, they’re especially convenient in freezer warehouses or cold storage facilities and, thus, are often employed by food businesses.
Case studies:
- Meat company Olot Meats has equipped its freezer warehouses in Spain with Movirack mobile racking.
- Saccheria F.lli Franceschetti has installed our Movirack mobile racks to store over 1,500 pallets in its production center in Italy.
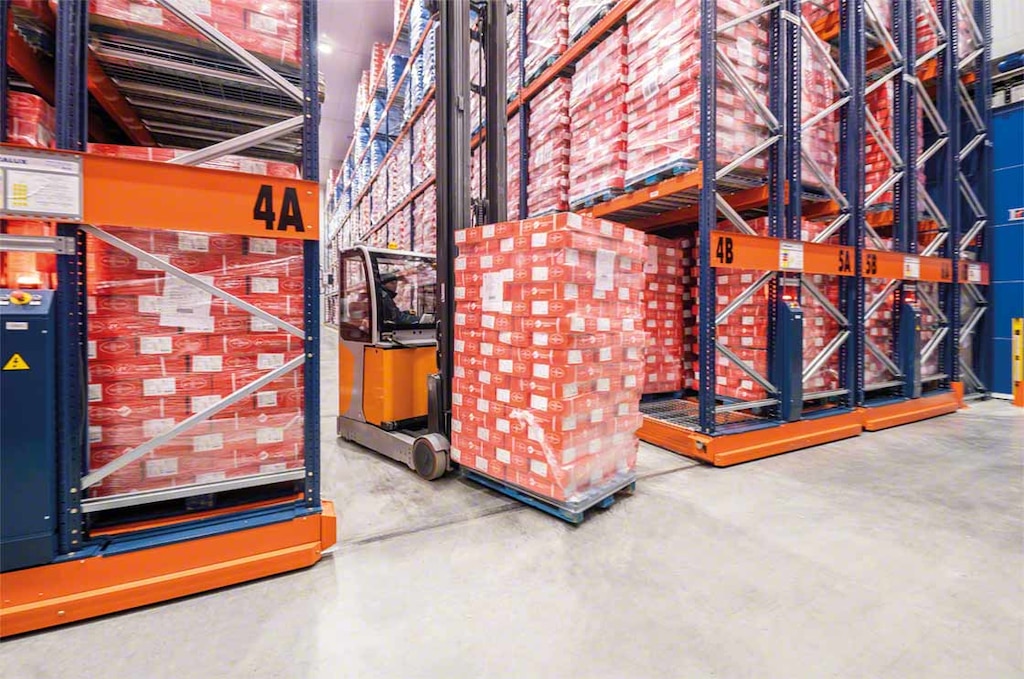
Cantilever racks
Cantilever racks are designed to store very long unit loads such as metal profiles, pipes, molding, lumber, metal and plastic sheets, etc.
They are composed of two columns to which load-bearing arms are attached. One of their particular features is that the arms are easily attached, so their position can be changed based on the size of the goods.
They are characterized by the fact that they offer direct access to the merchandise and by their versatility in storing any type of unit load, regardless of size. Consequently, they are seen in the warehouses of businesses that manage extra-long products (automotive, spare parts, home decor, and machinery and component companies, for example).
Case study:
- Ceramic giant Porcelanosa uses our company’s cantilever racks in its facility to manage bulky items.
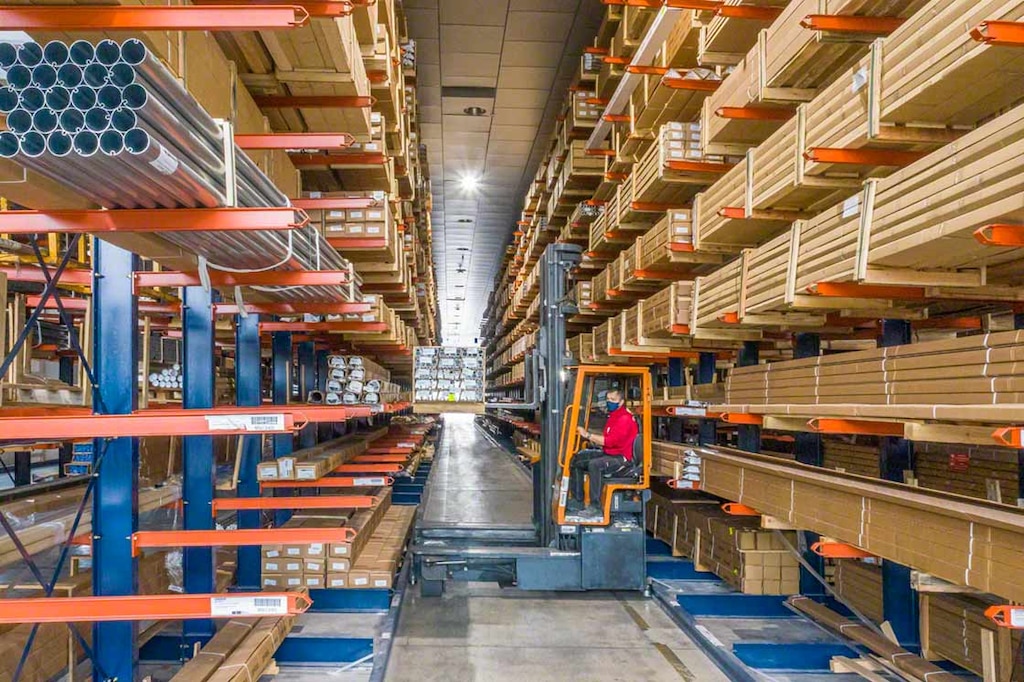
Compact racks
In contrast to racks providing direct access, these high-density racks make the most of the surface area and, therefore, offer a higher storage capacity. The following storage systems fall under this category:
Drive-in/drive-thru pallet racks
Geared towards homogeneous products with a large number of pallets per SKU, drive-in racks are constituted by racks with lanes formed inside them, equipped on both sides with support rails on which the loads are deposited. The forklifts drive inside these lanes with the load lifted above the level on which it will be deposited.
They are often implemented together with other storage systems (with pallet racks, for example). They are only used as a single system in facilities of manufacturers or logistics providers of raw materials or consumer products and in cold storage warehouses.
Case studies:
- Our company has provided Alifrut — a Chilean frozen fruit and vegetable provider — with four blocks of drive-in pallet racks in its freezer warehouse.
- Wholesale company Caromar has equipped its distribution center with 29' tall drive-in racks.
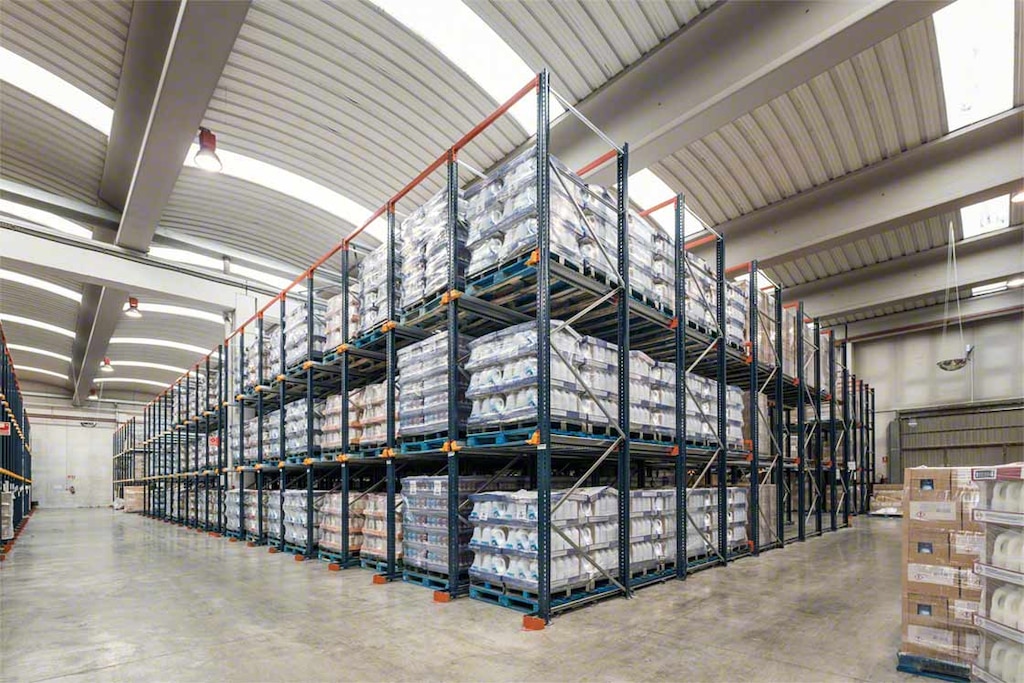
Push-back racks
Within the compact rack group, push-back racking systems (along with flow racks) provide more agility in goods management as well as better accessibility to the products.
The storage channels are set up on a slight incline so that the pallets can be pushed in. As the front part is lower than the back, when a pallet is removed, gravity moves the ones in the back forward towards the first position.
They’re a great option for products with few pallets per SKU and a high turnover.
Case studies:
- Agrochemical product company Desert Depot has outfitted its facility in Arizona with push-back racks with capacity for 16,000 pallets.
- College of DuPage has installed our push-back racks in its warehouse in Illinois.
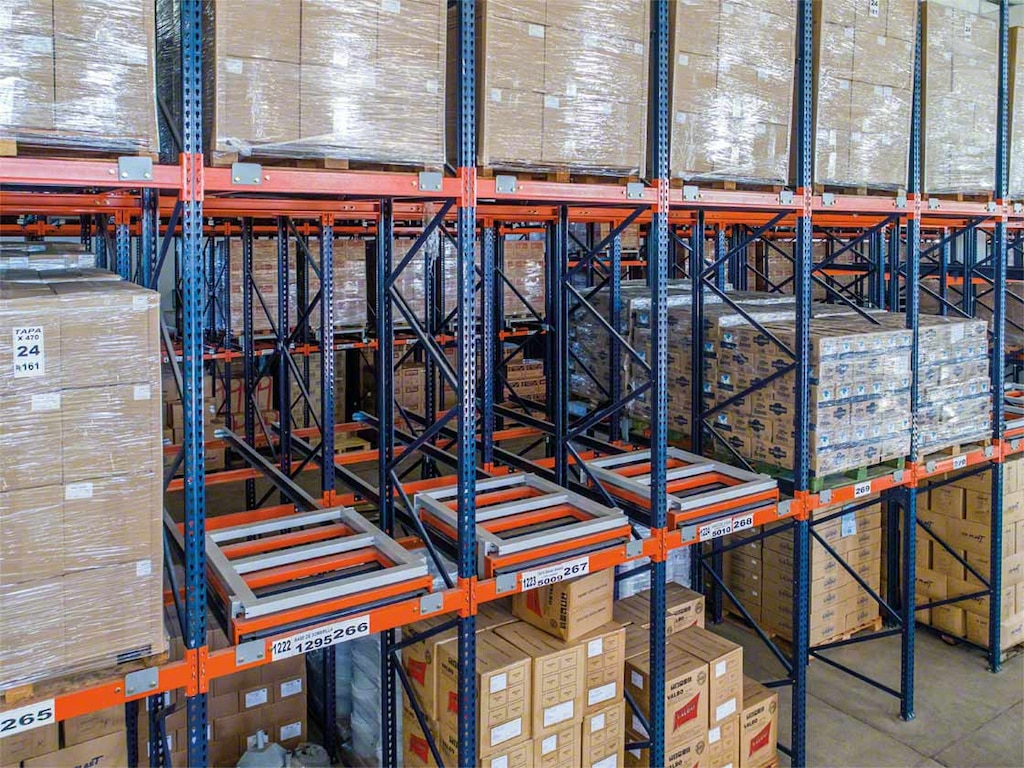
Racks with the Pallet Shuttle system
This solution incorporates a motorized shuttle charged with loading and unloading the pallets, increasing the productivity of the compact storage systems.
The Pallet Shuttle system is ideal for facilities with high-density storage of homogeneous products, in cold storage warehouses, in storage buffers, and for orders already prepared.
Case studies:
- Mecalux has equipped the facility of industrial service firm WISAG in Germany with two racking units with the Pallet Shuttle system, offering capacity for 16,000 pallets.
- Pharmaceutical company Medifarma has a rack-supported warehouse in Lima, Peru, consisting of racks with the Pallet Shuttle system to bolster its continuous growth.

Pallet flow racks
These are formed by slightly sloped channels equipped with rollers, enabling the pallets to move forward automatically by gravity and at a controlled speed.
As opposed to push-back racking, with these racks, the pallets are loaded on the higher end of the channel and move to the opposite end, ready for removal. The benefit of this solution is that it eliminates interference between the loading and unloading processes while facilitating management of the load in line with the FIFO principle (first in, first out).
Pallet flow racks are appropriate for facilities with perishable products. They can be set up between two working areas to streamline dispatches or can serve as a waiting area or storage buffer (for prepared orders, for instance).
Case studies:
- Pet food and accessories company Pet Supermarket manages all the products in its Florida warehouse with the help of pallet flow racks with capacity for 2,048 pallets.
- US tortilla products firm El Milagro has a facility with pallet flow racks offering a storage capacity of 700 pallets.
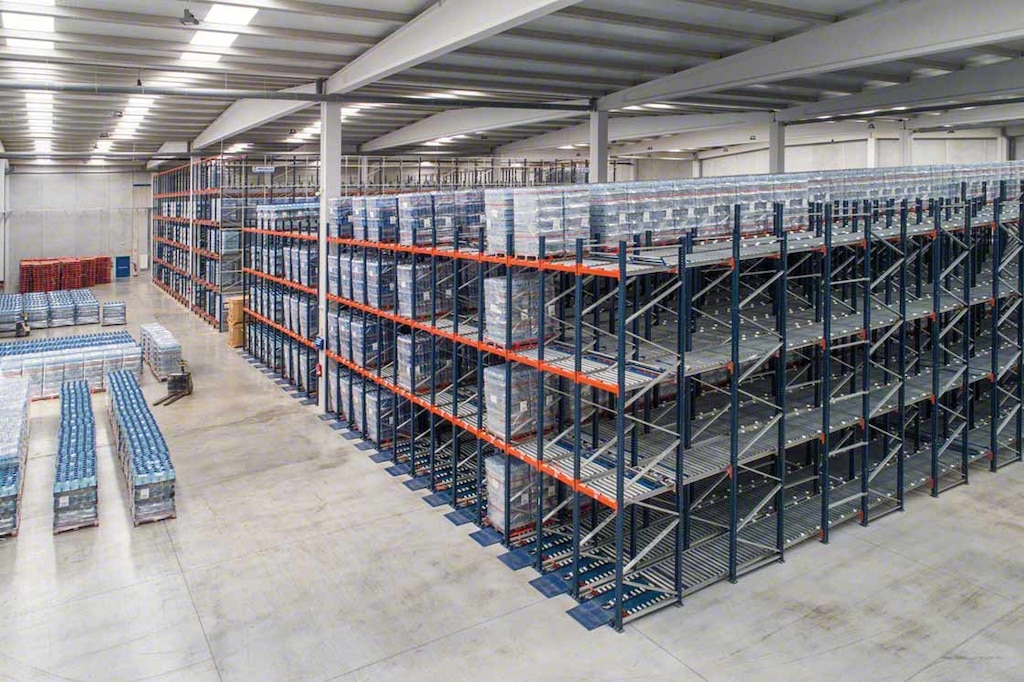
Automated storage and retrieval systems (AS/RS)
By automating your warehouse, you’ll increase productivity, agility, and safety in your facility, in addition to reducing costs.
Pallet racks, pallet flow racks, and the Pallet Shuttle system can be automated through the use of stacker cranes that insert and extract the pallets from their locations. The Pallet Shuttle system in particular can also incorporate transfer cars on each level to boost goods movement flows.
Stacker cranes require a narrower working aisle compared to standard forklifts, so more space can be allocated to the storage of goods. Likewise, they ensure continuous product entries and exits. For all of these reasons, automation is an extremely viable solution for managing high-turnover merchandise.
What about warehouses with boxes or small items?
Companies that handle small products and boxes tend to install carton flow racks for picking and wide span shelving for heavy loads. The main advantage is their flexibility and versatility, that is, the locations can easily be adapted to the size of the goods.
However, for much more agile and efficient management of these types of products, the best option is to install a miniload system (AS/RS for boxes). It consists of racks specifically designed to hold boxes and equipped with a stacker crane for boxes that inserts and removes the products from their locations automatically.
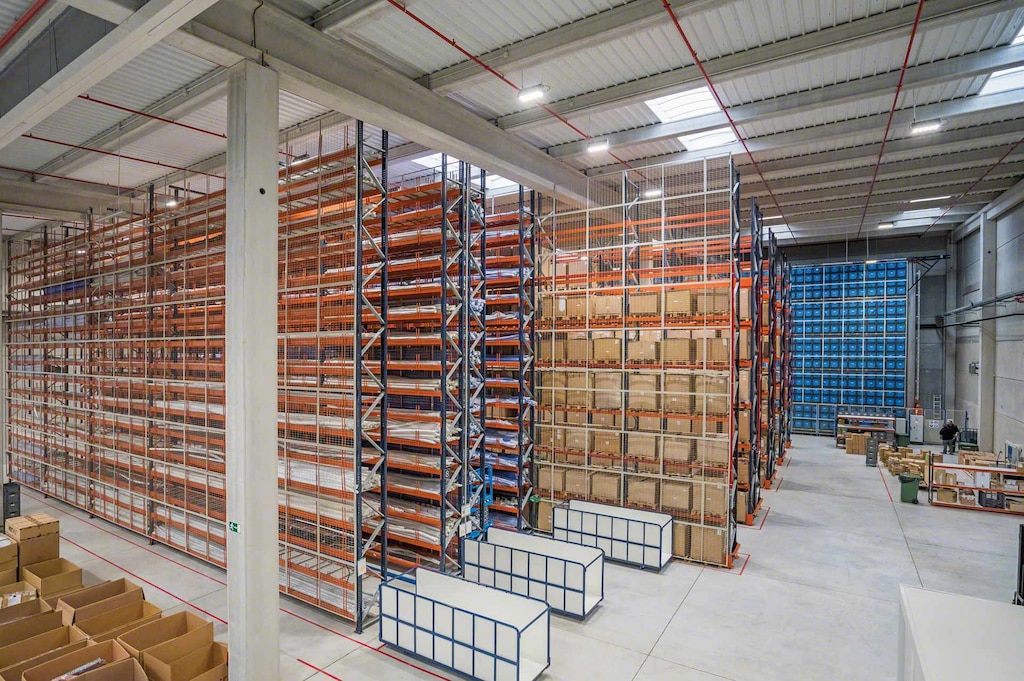
Criteria for choosing a storage system
The best storage system is the one that meets the needs and limitations of the warehouse in question in the most cost-effective way possible. When deciding on one, multiple factors should be considered, such as: expected storage capacity, number of SKUs and pallets per SKU, available space, handling equipment, and budget for the project.
Interlake Mecalux is a leading storage system manufacturer. Companies of all sectors manage their products using our racks. Be sure to get in touch. We’ll help you design the best warehousing solution for your logistics operations.