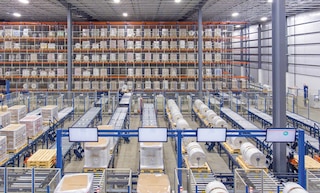
Warehouse stock: Classification and control
Warehouse stock is a vital part of logistics operations. Therefore, it’s essential to have clear visibility of this asset and distribute it effectively.
What is warehouse stock?
Commonly known as warehouse inventory, warehouse stock refers to the goods a company stores physically in a facility. These items represent investments made by the business to meet customer demands or production needs. They can consist of raw materials or finished goods, with the ultimate goal of generating profit through their sale or transformation. For this reason, selecting an appropriate classification method to organize inventory is fundamental. Other aspects to consider include the space this stock will occupy in the facility and the turnover of its various SKUs.
What are the different types of stock?
Product stock types depend on their characteristics. Within the same company, each item can follow a different policy. Warehouse stock can also be organized based on its function:
- Cycle stock. These goods are the staple items needed to satisfy regular demand volumes, without accounting for changes or unforeseen events in the supply chain.
- Seasonal stock. This inventory is accumulated to fulfill specific requirements during certain times or dates throughout the year. In e-commerce and retail, this may occur during Black Friday or Christmas.
- Safety stock. These products are ordered to cover exceptional situations, such as delays.
- Alert stock. This indicator notifies the business when it’s time to replenish a particular item. Ideally, its level should exceed that of safety stock.
- Dead stock. This includes damaged, obsolete, or unsellable items. The aim is to streamline internal logistics operations to keep inventory moving and prevent it from becoming dead stock.
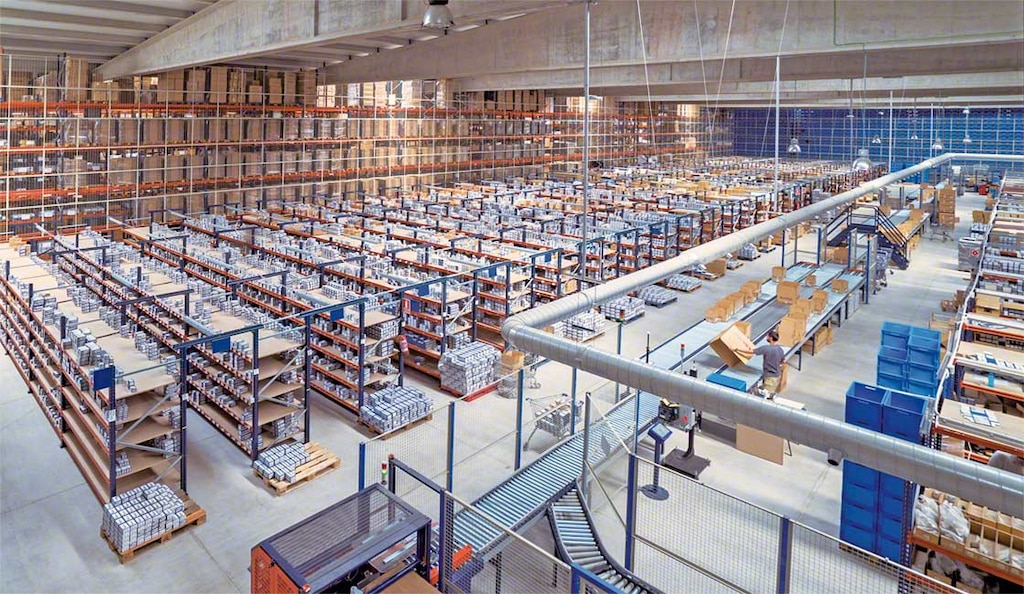
Similarly, warehouse inventory can be classified according to its purpose for the business and its operational organization:
- Physical stock: available inventory.
- Minimum stock: the products a company must have on hand to avoid stockouts and fulfill customer orders.
- Maximum stock: the facility’s total inventory capacity.
- Optimal stock: the ideal balance to meet business needs.
Warehouse stock control
Normally, each organization establishes a stock policy for managing the products in its facility. This policy determines, for instance, the number of days of available stock needed to meet customer demands or production requirements. Thus, the inventory control process involves tracking the goods entering and leaving the facility.
How to check stock in a warehouse
There are various ways to control inventory in a logistics facility. These range from manual methods to automated solutions that help companies stay competitive.
- Using a warehouse management system (WMS). A specific logistics software solution like the Easy WMS warehouse management system provides businesses with real-time information on the status of their stock. They know where it came from, its current location in the facility, and where it’s headed. This capability makes it easier to meet customer demands and ensure on-time, error-free deliveries. Moreover, the WMS can integrate with ERP systems to coordinate with manufacturing processes and oversee multiple warehouses simultaneously.
- Conducting physical inspections. Although software is the most effective option, visiting the facility — in line with the genchi genbutsu philosophy — is another way to identify products that have become obsolete or are experiencing inventory shrinkage.
- Reassessing inventory levels. Accurate demand forecasting indicates the time required to sell each item. However, shifting trends and unforeseen supply chain disruptions can cause imbalances. As a result, stock levels should be reevaluated as new information becomes available.
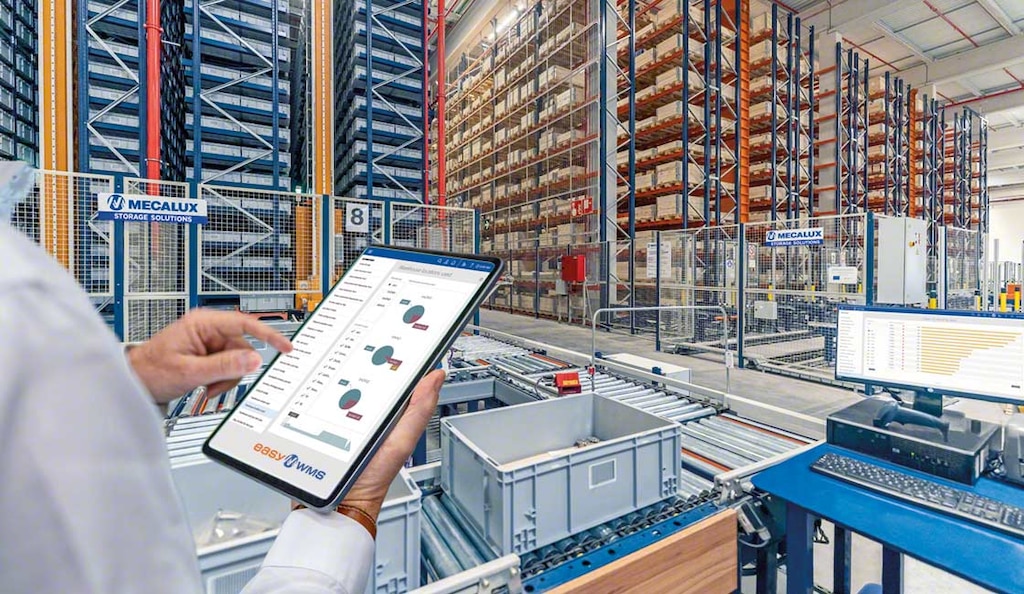
What is the reason for holding stock in a warehouse?
Although overstock should normally be kept to a minimum, an organization might want to accumulate inventory on-site for several reasons:
- Prevent stockouts. When customers can’t obtain the product they need, it often leads to lost sales and negatively impacts the company. Maintaining safety stock can help avoid this situation.
- Achieve objectives. Make to stock is a strategy organizations can use to anticipate situations or meet specific business targets.
- Reduce lead times. Having the products required to fulfill orders in the warehouse expedites the process, increasing consumer satisfaction and loyalty.
- Avoid last-minute costs. Storing extra inventory means not having to place urgent orders with suppliers.
- Meet seasonal demand. Toy companies, for instance, may accumulate stock in their facilities before Christmas to meet holiday season demand.
Control your warehouse stock with Interlake Mecalux
At Interlake Mecalux, we can help you integrate optimal solutions for housing your goods and collect valuable data about your logistics facility and inventory. In addition to streamlining operations, you’ll be able to make accurate predictions and anticipate scenarios. As automation experts, we created Easy WMS to control AS/RS operations, while our Easy DOM software provides visibility of large distribution networks. Contact us to leverage our company’s expertise in intralogistics solutions, built up since 1966.