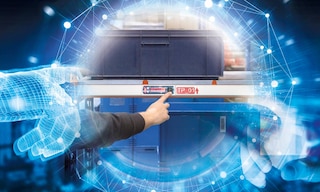
Warehouse ergonomics: 10 tips for improving safety
Warehouse ergonomics is crucial for operators to perform operations efficiently and for ensuring occupational safety in the workplace.
New technologies such as cobots, put/pick-to-light, and voice picking systems help to achieve warehouse ergonomics, benefiting both logistics managers and operators.
What is ergonomics and why is it important in a warehouse?
Ergonomics is the adaptation of the machines, equipment, and instruments people use to make their tasks more comfortable and effective.
Applied to warehousing and logistics, ergonomics encompasses a set of techniques and tools that facilitate operator activity to avoid risks. The most common ergonomic issues are related to manual load handling, awkward postures, and repetitive motions.
The aim of warehouse ergonomics is to guarantee the safety of the operators, the storage systems, and the goods handled.
10 tips for improving warehouse ergonomics
The following recommendations help to enhance warehouse ergonomics, in both automated and manually run facilities:
1. Adapt the building’s layout
The warehouse layout design should be tailored to the storage and order picking strategy employed. A well-designed facility optimizes operator movements, reduces internal transportation of goods, and facilitates access to the products required.
The design should also take into account the physical environment in which the operators work. That is, the equipment needs to be suitable, and the elements used by operators in performing their tasks should be within their reach.
2. Choose the ideal picking method
Determining in advance the order picking technique based on goods flows and product type not only enhances efficiency in the facility, but also improves the ergonomics of operators at their workstations.
Ergonomics in order picking is vital for preventing risks and ensuring operators’ well-being. Choosing the most suitable picking method ― wave picking, batch picking, or zone picking, among others ― will depend on the needs of each warehouse. Whatever the system, the workstations must be adapted to meet the appropriate ergonomics criteria.
3. Apply the goods-to-person picking strategy
With the goods-to-person approach, operators receive the products that make up an order automatically by means of automatic handling equipment such as pallet or box conveyors.
Thus, the operators remain at their workstations as the goods come to them, without having to travel or carry products, significantly improving warehouse ergonomics. Likewise, by bringing the product to the operator, this strategy shortens order prep times, increasing efficiency and reducing errors.
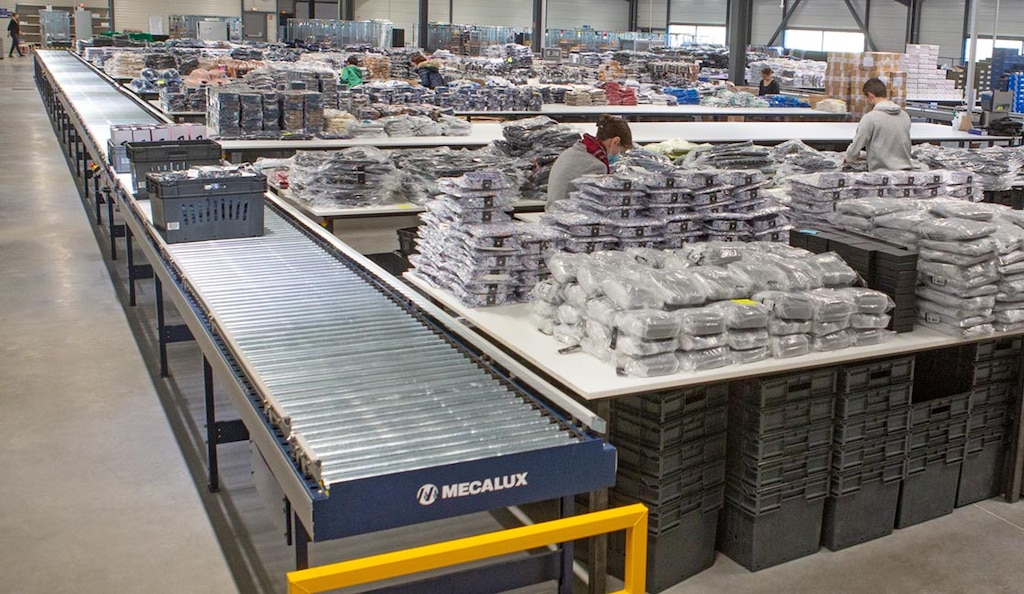
4. Assess the benefits of cross-docking
Cross-docking is an order fulfillment technique whereby goods are distributed directly to the end customer without having to be stored in the interim. This method, which requires the design of staging areas or specific storage systems that act as a buffer, optimizes internal movements of goods as well as the work of the operators.
How does this strategy affect warehouse ergonomics? Thanks to cross-docking, operators handle fewer products, avoiding repetitive and unnecessary motions that could cause them physical harm.
5. Employ picking assistance devices
To improve warehouse ergonomics, companies can also implement semi-automated order processing methods that make use of technology to facilitate the work of the operators.
Picking assistance technologies — e.g., pick-to-light, voice picking, and RF scanners — are effective because they’re connected to a warehouse management system (WMS). This program automates decision-making for operators, telling them step-by-step which operations to carry out.
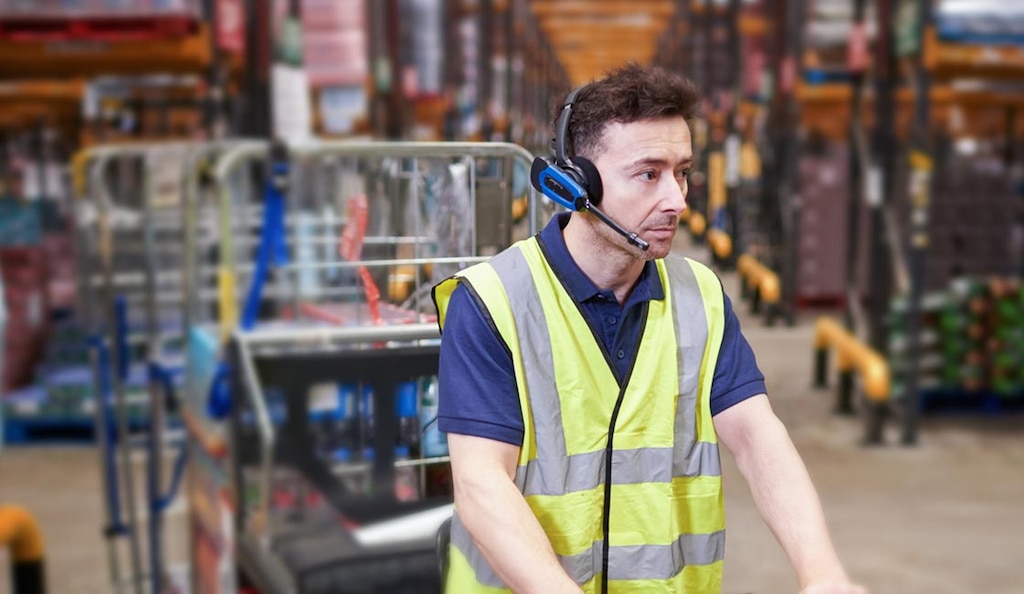
6. Automatize repetitive tasks
Replacing manual load handling with automated systems avoids risks to operators and optimizes the work done. To reduce the number of movements made in the facility, automated transport systems — i.e., conveyors, automatic guided vehicles (AGVs), and autonomous mobile robots — can be incorporated to move goods between the different points of the warehouse.
Carrying out pick and place operations with heavy goods can lead to ergonomic problems for operators. In this case, it’s advisable to install cobots (collaborative robots). Also known as anthropomorphic robots, cobots pick products and place them in or on their unit loads automatically and continuously.
7. Digitalize warehouse management
Deploying a warehouse management system (WMS) improves operator ergonomics by reducing the distances operators travel carrying goods in the facility during their workday. How does it do this? The software, for instance, designs optimized pick paths and efficient stock distribution (slotting) strategies.
At the same time, a WMS manages the picking assistance systems used by the operators. Through its connection with the RF scanners and other devices, the software organizes the different picking strategies and shows operators the steps to follow in this stage.
8. Use the right handling equipment
It’s critical to choose suitable material handling equipment because it will condition the layout of the facility, the number of operators required, and warehouse ergonomics.
Depending on the storage system(s) implemented, the goods housed, and the operations performed, one type of handling equipment or another will be needed. On an ergonomics level, for example, it’s better to pick small products with order pickers, since they can be raised to the desired height, avoiding awkward postures.
9. Train operators
Operators should be trained properly on the operation of the equipment, machines, and any support systems they use in their day-to-day. This training should include risk prevention. It’s very important for operators to be aware of workplace hazards so that accidents can be prevented.
In terms of software, Interlake Mecalux offers a customer training service that helps operators to make proper use of Easy WMS and its design and configuration tools, as well as the rest of Interlake Mecalux’s products.
10. Schedule regular technical inspections of storage systems
Technical inspections should be conducted by qualified technicians at periodic intervals to assess the condition of all warehousing elements in the facility.
In addition to this inspection, it’s a must to properly maintain and regularly survey the warehouse in order to ensure operator ergonomics. The working area should be sufficiently well lit and ventilated, and any unnecessary obstacles that could hinder daily operations should be removed. Industrial cleaning of the warehouse is fundamental for maintaining order in the workspaces and in goods handling.

Minimize risks, boost productivity
Warehouse ergonomics is key for improving operator productivity and avoiding risks in logistics facilities. Protecting employees and ensuring safety in the warehouse is a priority for all logistics managers.
Enhancing warehouse ergonomics involves employing the storage systems that best meet the needs of the business and the operators. Interlake Mecalux has extensive experience in installing the storage systems best adapted to the particular requirements of companies and their workers. Want to leverage the latest technology to get the most out of your logistics processes? Don’t hesitate to contact us. One of our expert consultants will offer you the best solution for your warehouse.