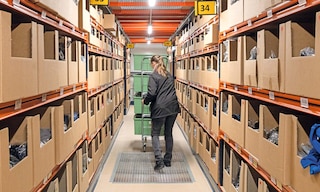
Warehouse picking best practices: 45 tips for optimization
Order picking tends to be one of the operations that causes the most headaches for warehouses. This is due to its complexity, its costs, and its risk of error, among a slew of other reasons. In this post, we give you 45 tips for warehouse picking best practices. Applied properly, they can help to reduce picking costs for companies, increasing agility, and, most importantly, limit mistakes in this logistics stage.
1. Design an efficient warehouse layout
The warehouse layout design must ensure that the picking areas are well delimited and organized according to the steps by which orders are prepared. These include the goods receipt, storage, replenishment, order picking, and packaging zones. It’s vital to coordinate operations so that no unnecessary movements are made.
2. Separate the picking and product returns areas
Companies often make the mistake of setting up the product return workstations close to the order preparation areas. Separating these two areas prevents loss of stock as well as uncontrolled inventory management.
3. Implement a WMS to digitize stock management
The deployment of warehouse management software ensures full product traceability and exhaustive control over order picking. The program organizes the different picking strategies, in addition to guiding operators step-by-step during this phase.
4. Slot the goods efficiently
The logistics manager should determine a set of SKU location rules and criteria based on actual order demand in the warehouse (turnover, product type, etc.). The implementation of a warehouse management system (WMS) minimizes the risk of error in this operation and optimizes slotting strategies.
5. Choose storage systems adapted to your warehouse
Logistics planning should include storage systems that best suit the characteristics of your logistics facility, the type of products stored in it, and flows of goods taking place in it.
6. Use carton flow racks to separate operations
Carton flow racks are ideal because they make it possible to increase the number of picking lines and cut down on operator travel. These storage systems boost the efficiency of single-unit picking.
7. Pallet picking
Pallet picking is an optimal solution when each pallet contains only one SKU. When carrying out order picking in this way, it’s recommended that high-consumption SKUs be placed on the lowest levels.
8. Design pick paths that maximize agility and effectiveness
Operator pick paths account for a high portion of order picking costs. Warehouse management software (such as Easy WMS from Interlake Mecalux) makes it possible to optimize operator routes taking into account picking and slotting methods predetermined by the logistics manager.
9. Allocate more space to picking
Compact storage systems — such as drive-in drive-thru pallet racks, mobile racking systems, and the Pallet Shuttle system — decrease storage space. As a result, more warehouse space can be dedicated to order picking.
10. Identify bottlenecks
It’s essential that logistics managers listen to their employees so that they can detect bottlenecks as well as improvements in order picking methods. Likewise, software such as the Labor Management System module from Easy WMS can help to detect inefficiencies and balance out operator workloads.
11. Integrate the WMS with the ERP system
Operations supervised by the WMS have to be aligned with your organization’s strategies. You have to sync the WMS with the ERP (enterprise resource planning) system to automatically transmit order information ― SKUs and delivery terms ― while ensuring two-way communication between the logistics department and other company units.
12. Monitor inventory in real time
Stock control is a key operation for efficient order picking. Digitizing inventory with a WMS is the best way to track warehouse stock in real time.
13. Replenish locations on time
When it comes to picking, there’s nothing more inefficient than arriving at a location you need to retrieve a product from and finding it empty. To optimize operator travel, it’s necessary to guarantee appropriate minimum stock levels (safety stock), ensuring that goods are continuously replenished in the storage locations.
14. Digitize and automate documentation
Manual order preparation entails management of basic documentation such as delivery notes, picking lists, and waybills. And doing this on paper leaves a business more open to error. A WMS automates, for instance, management of pick lists so that the operator only has to follow instructions from the software.
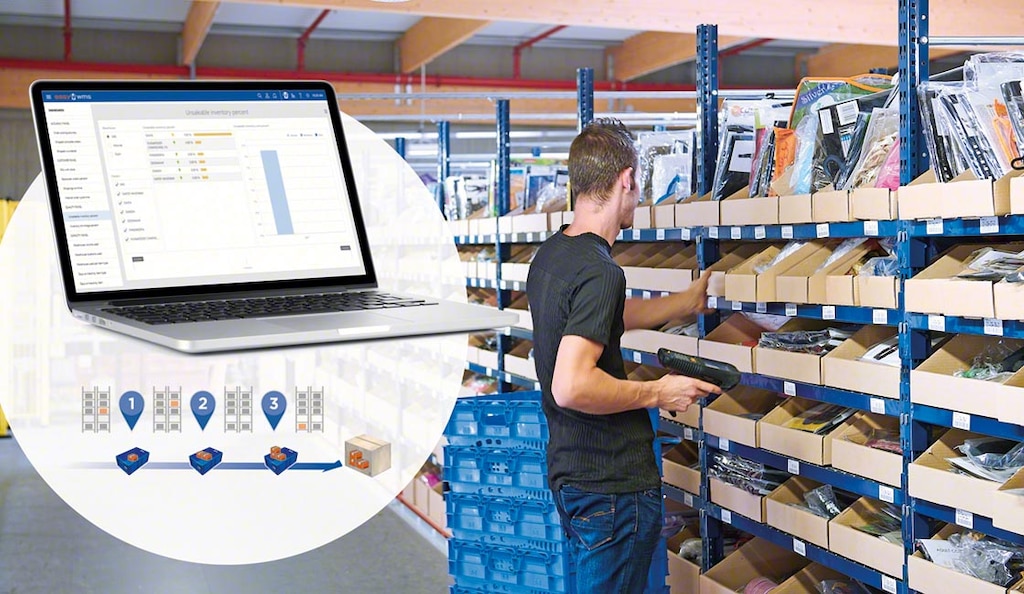
15. Define the best KPIs
The logistics manager should select the supply chain KPIs relating to order picking that best suit the type of business, product characteristics, and the various order prep strategies followed in the facility.
16. Automate performance measurement
To achieve maximum productivity in order picking, it’s essential to rely on a tool that automates data analysis. A program such as the Supply Chain Analytics Software module from Easy WMS provides logistics managers with real-time visibility of the actual throughput of the warehouse.
17. Calculate the internal order cycle time
This KPI determines how long it takes to fulfill an order. It’s measured from the time the order enters the WMS or ERP system until its completion. This calculation helps to control warehouse stock, order picking efficiency, and the quality of the logistics service provided to end customers.
18. Forecast changes in demand
Preset criteria and rules for product slotting need to be reviewed constantly so that you can detect changes in market trends, product seasonality, and demand peaks. Thanks to predictive analysis tools, you can forecast possible scenarios to make decisions based on the actual performance of the logistics facility.
19. Automate the flow of goods
Replacing manual handling equipment with automatic transportation systems such as conveyors for boxes speeds up the movement of goods to the pick stations.
20. Implement picking assistance solutions
One key tip for maximizing picking efficiency is to employ semi-automated order preparation methods. Systems such as pick-to-light and voice picking allow the warehouse management software to guide operators, showing them step-by-step which tasks to perform.
21. Explore robotics solutions
Pick and place robots complement picking, making it possible for operators to concentrate instead on value-adding tasks such as order personalization. Cobots (collaborative robots), meanwhile, are solutions that facilitate the work of operators, interacting with them and carrying out the more physical and cumbersome order prep tasks.
22. Automate picking with a goods-to-person system
Goods-to-person is an order preparation strategy whereby operators receive the goods automatically by means of automated transportation systems, e.g., pallet or box conveyors. The WMS is charged with coordinating the entire operation to guarantee efficient picking.
23. Improve goods receipt
An orderly, effective product receiving process expedites order picking. Operators in the goods receipt area are often equipped with RF (radiofrequency) scanners connected to the WMS; this enhances control when receiving stock and speeds up flows of product to the various storage and picking areas.
24. Adopt the right picking strategies
Determining which picking strategies you’ll use beforehand — based on goods flows and product type(s) — will boost efficiency in the facility. Some of the main order fulfillment methods include wave picking, batch picking, and zone picking.
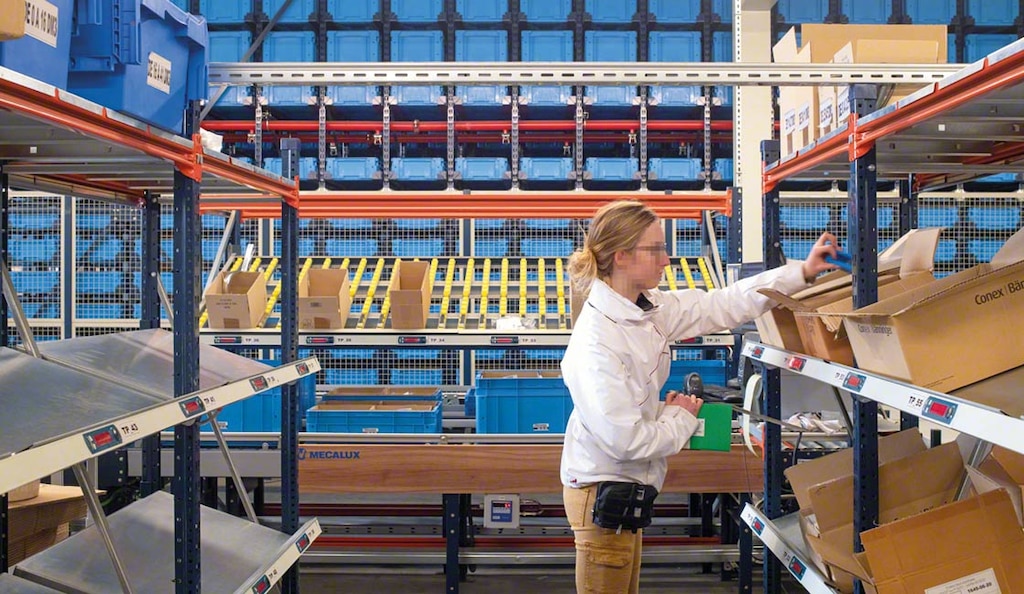
25. Try pick-to-box
One manual order prep method that can be highly cost-effective is pick-to-box. With this technique, operators retrieve items from the racks and place them into boxes on a cart. In doing so, they consolidate several orders simultaneously in the same boxes that will subsequently be used to ship them. This combines three different order fulfillment stages in one: picking, consolidation, and packaging.
26. Weigh the benefits of cross-docking
Cross-docking is an order picking technique that consists of distributing the goods directly to the end customer without storing them previously. This method requires the design of staging areas or specific storage systems that act as a temporary buffer for the products received.
27. Label products correctly
Improperly labeled merchandise can thwart the best picking strategies. Therefore, the logistics manager must validate the labeling process to ensure the system works well.
28. Apply a Lean philosophy
Lean logistics is a philosophy for organizing warehouse operations that aims to maximize efficiency in all processes, eliminating those that don’t add value. To achieve optimal productivity, you have to analyze order picking operations and determine which phases you can do without.
29. Eliminate unnecessary movements
To improve order picking, all movements and picks made by operators in the warehouse have to be streamlined. Any superfluous travel could mean an increase in the product’s logistics cost.
30. Structure the pick lists
When devising picking lists, it’s vital to consider the order in which the products on the list will be placed in the shipping box to make sure they’ll all fit. A WMS can sequence the movements so that larger SKUs are retrieved first.
31. Integrate product measurements in the WMS
Product weights and sizes can be entered into the warehouse management software to enhance accuracy in order picking. If, for example, a product unit is missing, the software will indicate that the order is incomplete.
32. Avoid placing multiple SKUs of different orders in the same cart
Putting several products belonging to different orders in the same cart increases the risk of error, especially when no picking assistance devices are used. Any mistake made during this operation could lead to longer order processing times and drive up costs.
33. Perform kitting before picking
To obtain maximum efficiency in order fulfillment, kit assembly should be done prior to order picking. If you can’t calculate the exact number of kits required, it’s a good idea to prepare a few beforehand.
34. Minimize product returns
A WMS is the ideal tool for eliminating the risk of error and minimizing product returns due to picking mistakes.
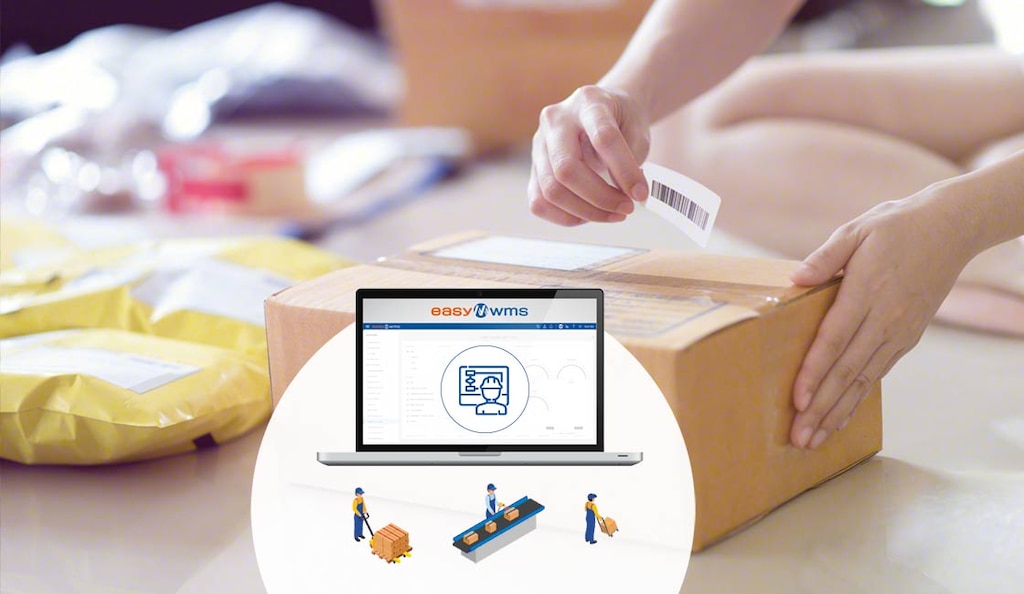
35. Ensure that all employees have the necessary equipment
Operators must have all the tools they need to carry out their tasks as quickly as possible: RF scanners, carts, pallet jacks, forklifts, etc.
36. Create ergonomic workstations
Pick stations require ergonomic designs that allow operators to work comfortably. These workstations should also be outfitted with all the working tools required to prevent unnecessary travel.
37. Ensure safety in the facility
Any process will be faster and more agile when the company fosters a safe industrial environment for the warehouse, the goods, and the operators. Order and cleanliness should be top priorities.
38. Signpost the warehouse properly
To ensure your facility is efficient and, above all, safe, it’s important to correctly mark the different sections. Operators, goods, and handling equipment — manual and/or automatic — all converge in the picking process, and inadequate signage could increase the risk of accidents.
39. Install suitable lighting solutions
The right warehouse lighting helps warehouse pickers to identify storage locations in addition to reinforcing safety in the facility. Lighting is a particularly critical factor in logistics centers with manually operated handling equipment
40. Train operators
For order picking to be efficient, it’s imperative to train operators on the use of the different storage systems, handling equipment, and even products. Pickers need to know the warehouse layout and signage like the back of their hand and be aware of any changes in product slotting.
41. Inform staff about strategies
Workers should understand the warehouse management strategies employed, knowing the reason why each operation is performed.
42. Implement gamification techniques
As in all work environments, strengthening motivation and competitiveness is an excellent way to achieve maximum throughput in a logistics facility. It’s more and more common to use gamification tools ― contests, picker of the month, etc.― to improve employee engagement.
43. Assess the support of a 3PL
In the face of unexpected spikes in demand, companies can outsource their logistics services to a 3PL (third-party logistics provider) that assists them with storage and picking operations.
44. Diversify strategies as your business grows
New market trends call for flexible warehouses that can adapt to changes in demand and to supply chain disruption. Organizations have to ensure elastic logistics and train operators to be ready for the unexpected.
45. Review logistics processes periodically
Warehouses require flexible logistics planning capable of continuously checking movement flows in order picking to adapt to changes in SKU types, in supply chain flows, and in order consolidation.
Highly efficient picking for modern times
Current consumer trends require boosting the efficiency of all logistics operations, particularly costlier ones like order picking. And e-commerce logistics standards (short delivery windows and free product returns, among others) are forcing warehouses to ramp up their pick station throughput. The implementation of warehouse management software ensures increased productivity in logistics facilities.
At Interlake Mecalux, we’re specialists in intralogistics storage solutions that enhance efficiency and productivity in the warehouse. Want to optimize your logistics and picking processes? Don’t hesitate to contact us; one of our expert advisors will offer you the best solution for your needs.